Insights in Mining Science & Technology - Juniper Publishers
Abstract
A process was developed for the beneficiation of a low-rank coal containing relatively high ash (25.97%) and sulphur (5.78%) content. The low-rank sub-bituminous coal of Makerwal Area, Surghar Range, Punjab Province, Pakistan was cleaned by froth flotation technology to get high quality clean coal for commercial applications. The main parameters of froth flotation technique such as grind size of coal, pH of the pulp, % solids of the pulp, agitation (impeller rotation speed), dosage of collector, frother and depressant and slurry conditioning time were optimized to get maximum grade and recovery of coal concentrate. Froth flotation tests showed that an overall recovery of 65% was achieved on weight basis. The final clean concentrate obtained at optimum conditions contained 7.80% ash and 1.37% sulphur content. The cumulative ash was reduced up to 70.15% and sulphur up to 76.29% in the final coal concentrate. It was blended with binder to form large size briquettes. The dried coal briquettes were found quite suitable for power generation and other heating purposes.
Keywords: Raw coal; Sub bituminous; Ash; Sulphur; Froth flotation; Clean coal; Grade; Recovery
Introduction
Coal is the most plentiful solid fossil fuel in the form of organic sedimentary rock that provides energy. Two third of the total world fossil fuel resources are in the form of coal. It is a major source of heat and energy in many industries. Its consumption rate is increasing day by day due to its cheapness. The usefulness of coal is well understood as it is used in many power generations plants to produce electricity [1]. It is converted into coke that is extensively used as a reducing agent in pyrometallurgical processes for reduction of metal oxides to produce metals.
Coal is not a homogenous substance. In fact, it is a heterogeneous composite of organic and inorganic substances. Carbon is the principal part of coal along with the other organic components such as hydrogen, oxygen and nitrogen and inorganic mineral matter. However, coal is the most polluting source of energy with respect to environmental concerns. The utilization of this energy source is damaging our environment with the emission of ozone depleting substances like CH4, CO2, SO2, and NO2. Carbon as a main constituent of coal is a major threat to the atmosphere and is responsible for climate change. Sulphur emission from coal combustion presents many environmental problems. The sulphur content in coal is categorized as elemental, organic, and inorganic. On combustion of coal sulphur combines with atmospheric oxygen to form sulphur dioxide and sulphur trioxide, which contribute to world environmental pollution in the form of acid rain. Both animals and plant life are affected due to this pollution [2].
Due to environmental consequences clean and effective coal utilization have become significantly necessary in recent years [3]. A variety of efforts are necessary to create and exhibit new clean coal technologies (CCTs) because a potential danger is created to environmental quality and human health due to the excessive use of coal. Various CCTs are being developed throughout the world to remove sulphur from the coal before, during and after combustion. The most used CCTs include coal-water slurry, micronized coal, limestone injection, gas reburning-sorbent injection, circulating fluidized bed combustion and flue gas desulphurization. These advance technologies have greatly helped in the reduction of sulphur from the coal [4].
The coal cleaning by physical methods reduces most of the objectionable impurities like ash and sulphur containing minerals from raw coal before combustion [5]. The common water based physical methods in practice are washing, scrubbing, sink-float or dense medium separation, gravity concentration and froth flotation [6]. The chemical methods using alkali and acid solutions are also used for the removal of unwanted impurities of ash and sulphur from coal, but these are costly [7]. Coal cleaning by bio-desulphurization using acidithiobacillus ferrooxidans microorganisms is also in use [8]. The coal cleaning prior to utilization results in lower sulphur dioxide emissions minimizes non-combustible mineral matter (ash) and improves thermal efficiencies [9].
The coal fields of Makerwal lies in the Surghar Range (Trans-Indus Range) that consists of entirely sedimentary rocks. The coal fields start from 3km west of Makerwal town and continue to 13km west of Kalabagh city and cover an area of around 75 km2 in district Mianwali, Punjab Province of Pakistan. Makerwal coal mines are located at 32°N latitude and 71°E longitudes and lies at a height 311 meters from sea level. The total estimated reserves possible for development are more than 22 million tons [10]. But these deposits are of low quality containing high amount of sulphur and ash content and low heating value. Coal cleaning is required before putting them in to an effective use.
This paper describes the physical coal cleaning tests conducted on Makerwal coal to utilize these vast resources of coal. The objective is to develop an efficient and cost-effective process for up-gradation of low rank coal into a concentrate with acceptable limits for utilization in industries. The study is especially focused on to reduce sulphur and ash content to a minimum level so that thermal efficiency can be improved along with control on pollution problem.
Materials and Methods
Sample Collection
A bulk sample of coal was obtained from coal mines near Makerwal Town, Tehsil Isakhel, District Mianwali. The coal is produced from a single bed that ranges in thickness from 2 to 10 feet with an average of 4 feet. Two bags of representative coal sample weighing 50 kg each was collected from the main Makerwal area. The coal sample was composed of about 60% powder material while the remaining sample was in the form of lumps having variable size ranging from 1-8 inch. The colour of lumps varied from jet black to dull brownish. Most of the lumps exhibited the friable nature while powder coal was hard and compact.
Sample Preparation
The as-received coal sample was crushed in Mineral Processing Laboratory of MPRC, PCSIR Lahore by lab size jaw crusher to about half inch downsize. It was further crushed in roll crusher to achieve quarter inch downsize. The head sample of coal was prepared by coning-quartering and riffling of crushed coal. It was pulverized in disc pulverizer to obtain minus 60 mesh size for evaluation. The rest of coal was packed in plastic bags for laboratory scale beneficiation tests.
Coal Evaluation
The representative sample of coal was evaluated by proximate analysis, sulphur and gross calorific value (GCV) on as-received basis. ASTM Standard procedures were adopted for analysis. Total moisture in the coal was determined by heating the coal sample in electric oven at 105oC till constant weight in accordance with ASTM Standard D-3172. Ash content was determined by gradual but complete combustion of weighed coal sample in the presence of excess of air supply in electric muffle furnace at 750oC. Volatile matter of coal was determined by heating the coal at 930oC for 7 minutes under controlled conditions. Fixed carbon was calculated by applying formula. Total sulphur in the coal was estimated gravimetrically by Eschka mixture fusion and precipitation of sulphur as BaSO4 according to ASTM D-3177. The gross calorific value (GCV) was determined using Bomb Calorimeter by standard procedure described in ASTM D-5865. Similarly, evaluation of the processed products of flotation tests and final briquetted coal was performed. The proximate analysis, sulphur and gross calorific value of the head sample of coal are presented in Table 1.
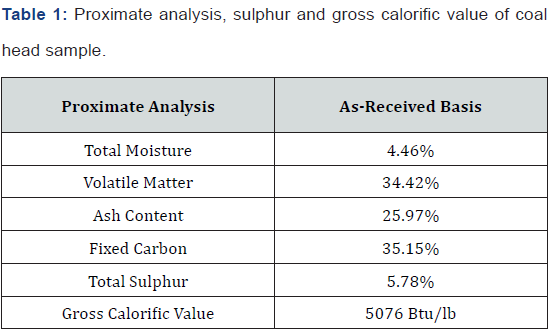
The chemical analysis of ash was performed by conventional methods. The coal ash was fused with soda ash at 900°C for 1 hour and leached in dilute HCl for evaluation of elements. Silica and alumina were estimated gravimetrically while other elements were determined volumetrically. Alkali metals (only sodium and potassium) were found using Flame Photometer (Model: PFP-7, Make: Jenway, England). The complete chemical analysis of coal ash is shown in Table 2.
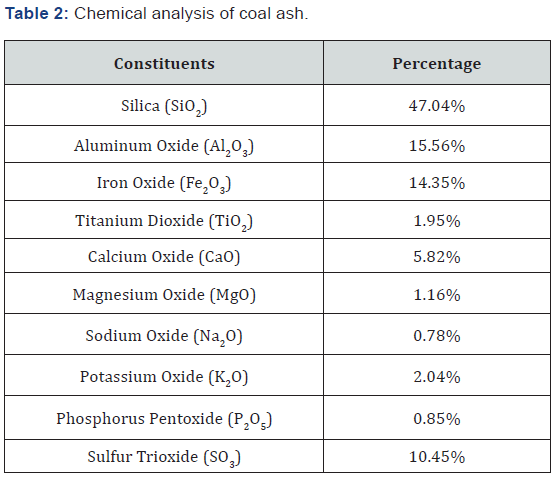
Froth Flotation Tests
Froth flotation tests were performed on coal sample using batch type Flotation Machine (Model: D-12, Make: Denver, USA). The feed for flotation tests was prepared by wet grinding of crushed coal in rod mill (9"×18") with liquid to solid ratio of 1:1. The ground coal was carefully shifted to stainless steel flotation cell of 1 Litre capacity. Flotation tests were carried out on laboratory scale to optimize important parameters of flotation. The particle size of the coal was changed from minus 100 to 250 mesh. The pH of pulp was varied between 7 and 10 with lime. The percentage of solids in the slurry (pulp density) was studied by varying it from 20% to 35%. The impeller speed (agitation) was varied from 900 to 1200 rpm. The dosages of flotation reagents (collector, frother, and depressor) were also investigated. The conditioning time period of slurry was also varied from 5 to 20 min. The optimum conditions of typical flotation test are reported in Table 3 while the material balance is summarized in Table 4. The proximate analysis, sulphur and gross calorific value of rougher and cleaner flotation concentrates are shown in Table 5 (Figure 1).
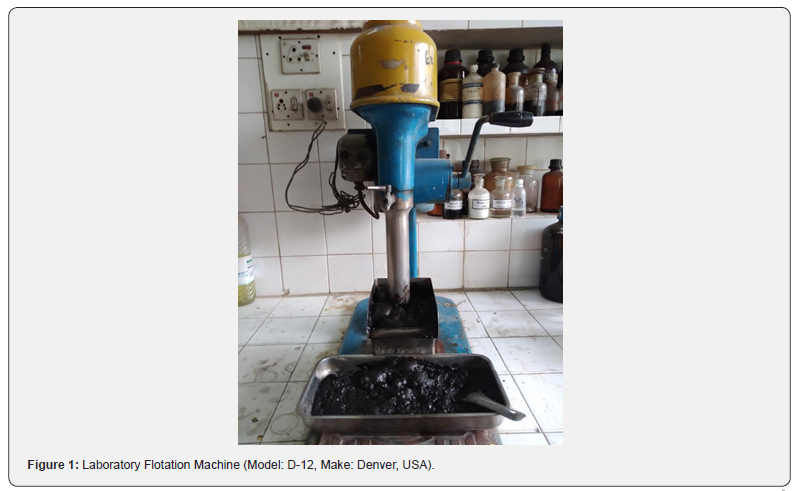
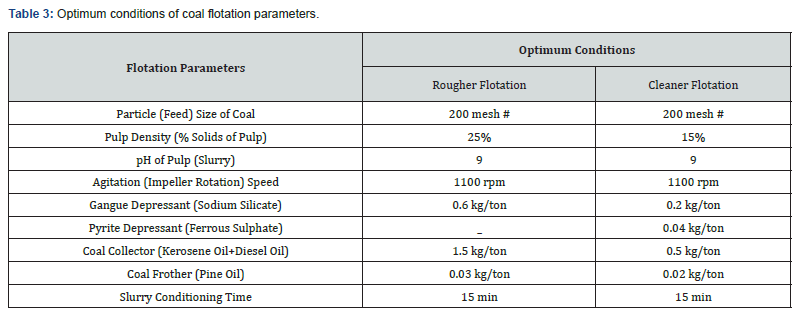
Briquetting of Coal
Fine clean coal concentrate obtained after flotation test was filtered to remove water and then dried in electric oven at 105oC to get rid of moisture and flotation reagents. It was mixed with appropriate amount of binder in a trough mixer to make briquettes of about one inch. Different types of binders were tried. The coal was mixed with
a) 2% molasses and 2% lime
b) 2% sodium silicate and 2% lime
c) 2% soda ash and water
d) 8% coal tar pitch binder
e) 6% molten asphalt binder
The coal briquettes were made by pressing the thoroughly mixed coal-binder mixture in roll type briquetting machines (Local). These were cooled down to room temperature to get final briquettes.
Results and Discussion
Chemical Composition
The composition of coal on as-received basis is shown in Table 1. It is obvious from this table that coal contains 4.46% total moisture, 34.42% volatile matter, 25.97% ash content, 35.15% fixed carbon and 5.78% sulphur and calorific value of 5,076 Btu/Ib. The fixed carbon value (35.15%) of the coal is sufficient to exploit it for commercial utilization. Relatively high value of ash (25.97%) depicts the significant amount of mineral matter contaminated in the coal. The low gross calorific value (5076 Btu/lb) of pulverized coal sample indicates the presence of less amount of combustible matter and high amount of gangue components. The ultimate analysis (sulphur only) shows that it has 5.78% total sulphur which is also on the higher side. These results show that the coal under investigation ranks as sub-bituminous containing high amount of volatile matter (34.42%).
The coal is a heterogeneous mixture of organic and inorganic matter. During combustion of coal, the organic matter burnt away while inorganic mineral matter is converted into ash by chemical reactions. Composition of coal ash depends upon the nature of minerals contaminated in the coal. Table 2 shows the chemical analysis of coal ash. The high iron oxide content (14.35%) and sulphur content as sulphur trioxide (10.45%) in ash indicates the presence of pyrite and sulphate (inorganic sulphur). The significant amount of silica (47.04%), alumina (15.56%), soda (0.87%) and potash (2.04%) also predict the presence of clay minerals and silicates in coal.
Selection of the process
The raw coal is a mixture of coal particles and non-combustible matter (impurities). The unwanted impurities in the coal may be categorized as inherent and removable [11]. The inherent impurities cannot be removed from the coal by physical methods because these are organically attached with the coal. However, the removable impurities can be separated using physical coal cleaning processes. Depending upon the nature of impurities, different processing methods are in practice to clean coal prior to its utilization. Froth flotation is a surface-based process which depends upon surface wettability and hydrophobicity of coal and associated minerals [12]. It was selected to remove unwanted impurities of sulphur bearing and ash forming minerals from coal under investigation. The coal was subjected to bench scale froth flotation tests to obtain high quality clean coal. The coal was made hydrophobic and associated minerals hydrophilic by various flotation reagents.
Effect of feed size
The particle size of flotation feed is a decisive parameter [13]. The effect of feed size on the removal of ash and sulphur bearing minerals from the coal was investigated using different feed sizes. The crushed coal was ground in rod mill with liquid to solid ratio of 1:1 to achieve different feed sizes. The flotation tests were performed on feed size of nearly 100 % minus 100, 150, 200 and 250 mesh (BSS). The initial tests were carried out on arbitrarily selected values. The results of these flotation tests in term of reduction in ash and sulphur contents are reported in Figure 2. It can be noted that the particle size of coal has a significant impact on removal mineral contaminants [14]. The higher ash and sulphur content at coarser particle size indicates that it still contains some degree of locked particles which require more grinding for liberation [15]. As the coal size was reduced, a gradual decrease in the ash and sulphur content was observed in the coal concentrates. It can be noted that the finer grind size of coal results in the more release of mineral impurities from the coal. The best rejection of ash (11.23%) and sulphur (3.16%) was observed at the feed size of minus 200 mesh size (75µm). This feed size was opted for onward tests. After that both ash and sulphur content increased slightly which indicates that finer size generate slimes of various impurities which contaminate the coal concentrate.
Effect of pulp density
The percentage of solids in the slurry (pulp density) is another influential parameter of flotation [1]. In this set of experiments, pulp density of coal was varied as 20%, 25%, 30% and 35% to study its effect on the rejection of ash and sulphur from the coal. The results of these tests are illustrated in Figure 3. It was noted that when the pulp density was increased from 20% to 25% solids, the quality of concentrate was improved, but as it was further increased to 30% it degraded. The optimum rejection of ash (11.05%) and sulphur (2.91%) was achieved using a pulp density of 25%. This pulp density was selected for further parameters studies. The grade of coal concentrate dropped above this pulp density due to the fact that the larger amount of feed hinders the proper attachment of the reagents over the mineral particles leading to some contamination of gangue minerals in coal concentrate. Moreover, thick froth layer was produced at higher pulp density and the draining out of entrapped gangue particles from the thick froth was more difficult. So, in the latter trials, the pulp density was set at 25% solids.
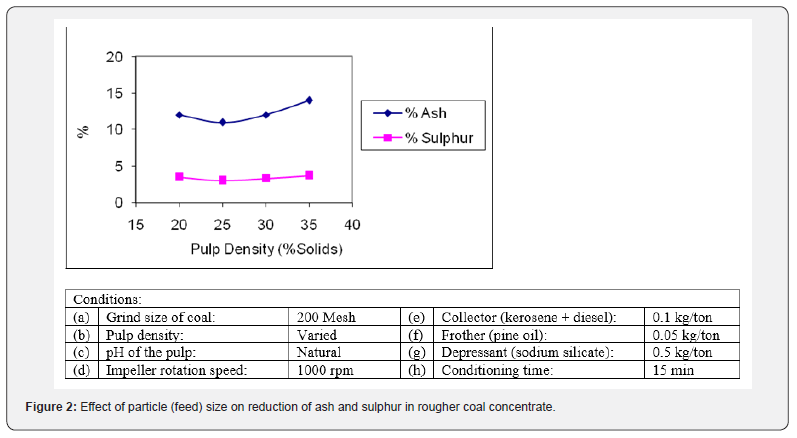
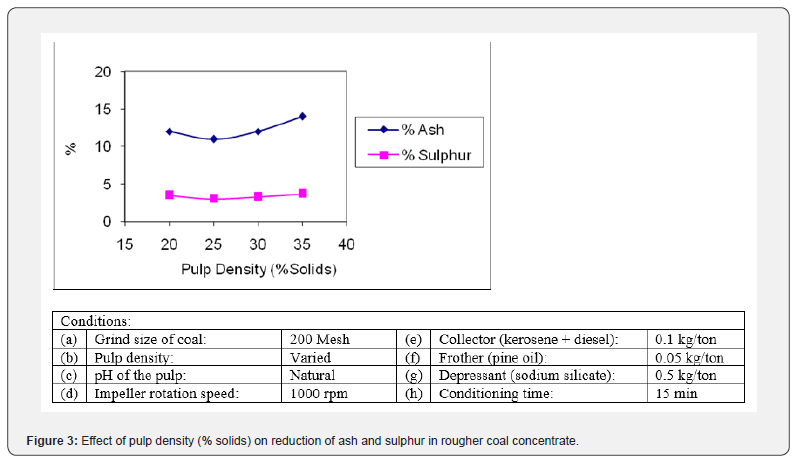
Effect of pulp pH
The pH of pulp is a crucial parameter of flotation as it helps in proper attachment of different flotation reagents on mineral particles (collector-mineral bond). The effect of pH of pulp on the performance of collector was studied by varying it from 7 to 10. The pH was adjusted with lime. The reason for using lime as pH modifier for flotation of coal fines is that it had also a depressing effect on pyrite particles. Pyrite often floats and report to the froth due to its inherent hydrophobic nature [16]. Lime depresses pyrite from flotation by hydrolyzing it. The results of these flotation tests are plotted in Figure 4. These tests revealed that a slightly alkaline pH of slurry gave the maximum grade (quality) and recovery (quantity) of coal concentrate by highest rejection of sulphur and ash bearing minerals. At pH 9, the percentage of ash was reduced to 10.88% and sulphur 2.73% respectively. The reason could be explained that at around pH 9 the ionization is 1:1 ion complex and the net adsorbed ion charges is zero. The surface of the coal particles for the adsorption of the collector is saturated with collector [17]. At this pH, the mineral-collector bond is more stable. So, the pH of pulp was maintained at 9 in the latter flotation tests.
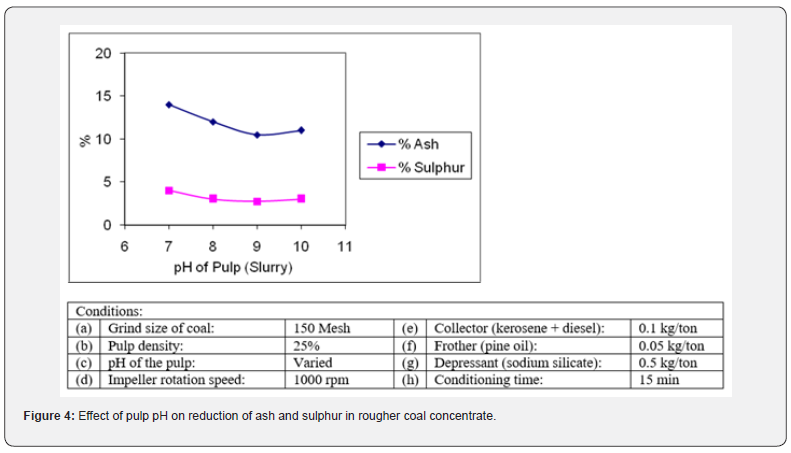
Effect of Agitation
The agitation of pulp and aeration is another key parameter of flotation process. To observe its effect a few flotation tests were carried out by varying the agitation speed and keeping other variables constant. The results were plotted in Figure 5 as agitation speed versus % reduction in sulphur and ash content. It was found that the best ash (10.63% and sulphur (2.64%) rejection in the coal concentrate was obtained at agitation speed of 1100 rpm which indicates the adequate mixing and aeration in the pulp. It was fixed at 1100 rpm in subsequent experiments. It was noted that at lower agitation, the height of froth surface remained low so skimming of froth from the surface was not proper leading to poor yield. On the other hand, the higher agitation (above 1100rpm) spilled the froth along with some pulp into the launder resulting in lower grade.
Effect of collector dosage
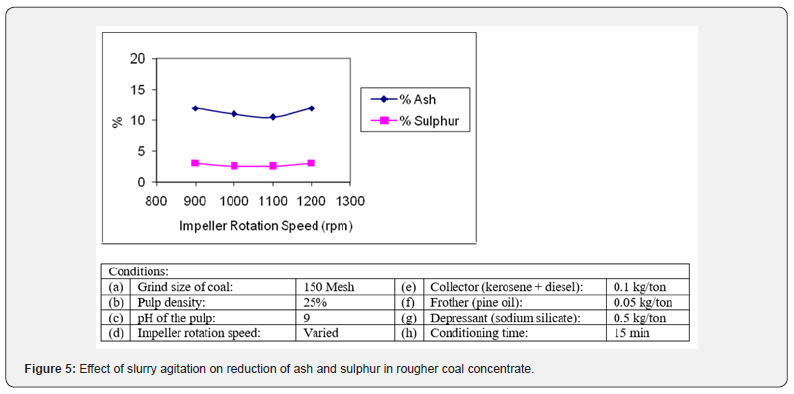
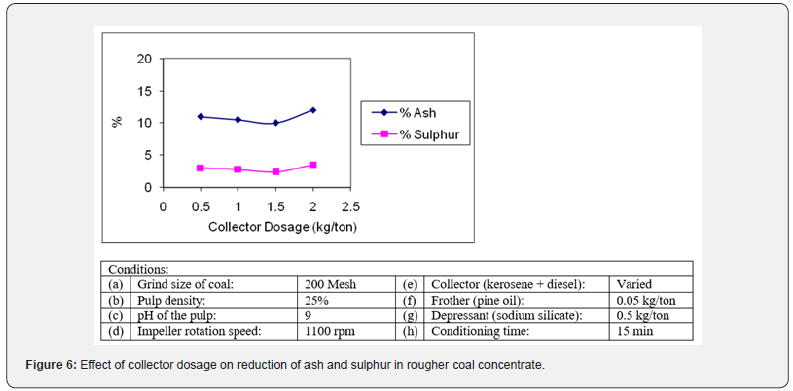
Selection of appropriate flotation reagents is critical in flotation process [18]. Different types of collectors are used for the flotation of coal [19]. In preliminary experiments, oleic acid was employed as collector for the flotation of coal to check the response, but the flotation recovery was found poor. It seems that oleic acid is a weaker collector and is not very selective. Later, diesel oil and kerosene oil were tried separately and in combination for flotation of coal in natural and basic pH range and the flotation behavior of the coal was noted. A combination of diesel oil and kerosene oil (1:1) was found to be a better collector for the flotation of coal under investigation than either collector alone [20]. It was observed that a mixture of kerosene oil and diesel oil is more selective collector for coal due to its hydrophobic nature and gave much higher recoveries. It could be inferred from the flotation results that the mixture of reagent shows synergism and dominates over single surfactant [6]. The floatability of coal samples was investigated by using 0.5- 2.0 kg/ton of collector mixture (1:1). The ash and sulphur reduction data obtained was plotted in the Figure 6. The concentrate yield improved as the concentration of collector was raised from 0.5 kg/ton to 1.5 kg/ton. The collector produced the best result showing the maximum removal of ash (10.06%) and sulphur (2.54%) ion the rougher concentrate at a concentration of 1.5 kg/ton and after that performance is declined. So, it was considered as the optimum value. It corresponds to the starvation level i.e., the concentration required for making the monomolecular layer of collector on surface of coal particles [21]. The further increase in concentration of collector tends to reduce the selectivity by collecting and floating other minerals. The flotation results could be explained by the emulsification and adsorption behavior of the reagents [22].
Effect of frother dosage
In a few earlier experiments, different frothers such as cresol, methyl isobutyl carbinol, polypropylene glycol and pine oil were tried to study the effect of frother on flotation behavior of coal [23]. It was noted that the pine oil produced more stable froth in the flotation of coal. It adsorbs on coal surface and has collecting properties for coal [24]. A series of flotation tests were carried out using pine oil as frother. Various dosages of frother ranging from 0.01-0.05 kg/ton were employed and its effect on the grade and recovery of coal concentrate was studied. The results obtained are shown graphically in Figure 7. It is evident that the rougher coal concentrate with the lowest ash (9.98%) and sulphur (2.47%) was obtained with 0.03 kg/ton of pine oil. At low dosage of frother, the strength of air bubbles was so weak that coal particles could not be carried to the froth phase and resulted in lower yield. The higher dosage (0.05 kg/ton) of frother could not improve the result.
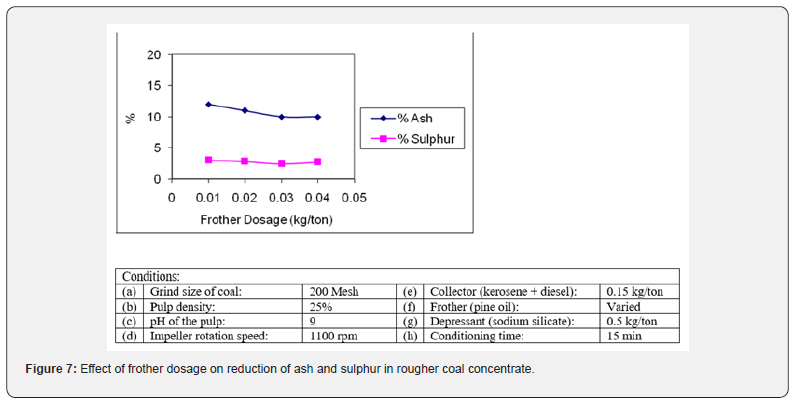
Effect of depressant
The selection of suitable depressant plays a deciding role for the rejection of impurities from coal [25]. The major gangue minerals present in coal under investigation were different types of silicate minerals such as quartz, shale, slate and clays. Similarly, the pyrite and gypsum (calcium sulphate) were the main unwanted sulphur containing minerals. Sodium silicate (water glass) was added to depress the siliceous gangue minerals [21]. The results were plotted in Figure 8. It was found that best results in term of ash and sulphur rejection were obtained using 0.6 kg/ton of sodium silicate. The ash and sulphur content of rougher coal concentrate could not be reduced below 9.75% and 2.38% respectively at any further quantity of depressant. The pyrite and various sulphate minerals were depressed using iron (II) sulphate as depressant at cleaning stage.
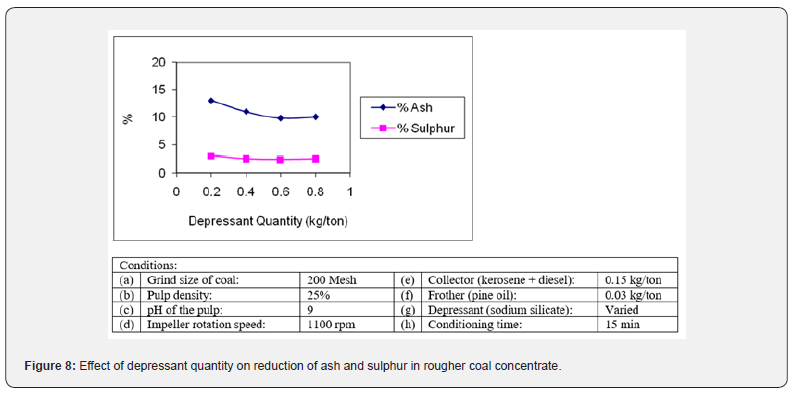
Effect of conditioning period
The conditioning time of slurry has a significant effect on the quality and quantity of the flotation products [26]. To determine the optimum conditioning period, it was varied from 5 to 20 minutes with increment step of 5 minutes. The results obtained in the form of ash and sulphur reduction are presented in Figure 9. It is observed that a conditioning time of 15 minute is sufficient for an optimum contact of the reagents with the mineral particles for maximum removal of impurities from the flotation product. The rougher concentrate contained 9.69% ash, 2.27% sulphur content. It was also noted that prolong conditioning time does not improve the results [27].
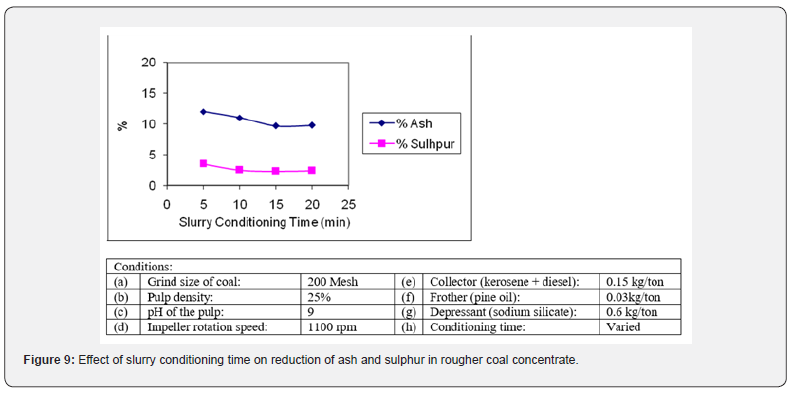
Effect of cleaning flotation
The rougher concentrate was cleaned by another flotation. The cleaner flotation tests were carried out under the same conditions as were used for rougher flotation except the quantity of some flotation reagents. In the cleaning flotation tests, additional quantities of flotation reagents were added to further clean the coal particles from associated gangue minerals (Table 3). In the cleaning tests, a small amount of ferrous sulphate (0.04kg/ton) was added to depress pyrite and sulphate minerals (gypsum etc.). The pulp density was also lowered from 25% to 15% to improve the results. The cleaning of rougher concentrate results in higher rejections of undesirable impurities of both ash-forming and sulphur bearing minerals as compared to conventional single step rougher flotation (Table 5). By using two stage process i.e., rougher and cleaning flotation, a greater range of impurities were removed at higher overall separation efficiency. This strategy was found quite suitable for rejection of mineral matter with minimal loss of heating value to desirable limits in the coal.
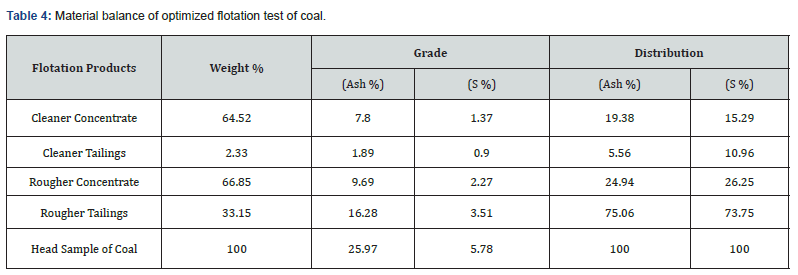
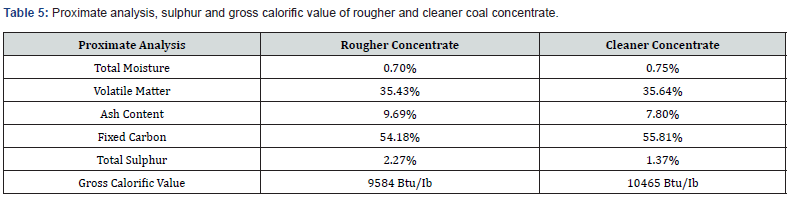
Material balance calculation
The optimum conditions of a typical coal froth flotation test given in Table 3 describe that the rougher flotation coal concentrate was achieved using a coal size of almost 100 % passing 200 mesh, pulp pH of 9, pulp density of 25%, agitation speed of 1100rpm, collector dosage of 1.5 kg/ton, forther dosage of 0.03 kg/ton, depressor quantity of 0.6 kg/ton and conditioning time of 15 minutes. The material balance calculation of a typical flotation test (Table 4) indicates that the rougher coal concentrate containing 54.18% fixed carbon was achieved with 66.85% recovery on weight basis at optimum conditions. After one cleaning flotation it is possible to attain a high-quality clean coal concentrate containing 55.81% fixed carbon with 64.52% weight recovery from low rank coal assaying 35.15% fixed carbon. As a result of flotation tests, the cumulative ash of the raw coal was reduced from 25.97% to 7.80% and sulphur from 5.78% to 1.37% in the final coal concentrate. Consequently, the percentage of fixed carbon (grade) of the coal improved from 35.15% to 55.81%. Based on these results, it can be said that the coal sample under study is amenable to cleaning by froth flotation process. The flotation process was proved an effective technique for rejecting ash and sulphur containing minerals from raw coal and recovering a clean coal for commercial purpose.
Composition of coal concentrate
The proximate analysis of final clean coal concentrate presented in (Table 5) shows that it contains 0.75% moisture, 55.81% fixed carbon, 35.64% volatile matter, 7.80% ash and 1.37% sulphur and its gross calorific value of coal was 10465 Btu/lb. It is obvious from the results that it contains minor quantity of ash (7.80%) and sulphur (1.37%) as impurities as compared to 25.97% ash and 5.78% sulphur in the original raw sample. The flotation process gave outstanding performance for the ash and sulphur rejection from the raw coal. The proximate analysis of final flotation concentrate envisages that it is suitable for industrial utilization especially in cement industry.
The fine sized clean coal product obtained by froth flotation can be directly used to meet the requirement of energy or it can be briquetted into suitable size for commercial purpose. The different kinds of binders were tried to produce large size coal. It was observed that the properties of the briquettes were largely dependent upon the kind of binder used. The lime-molasses mixture was found to be the best binder. It has advantage in the production of porous structure of coal briquettes. Lime also reduces emission of sulphur dioxide into environments. Moreover, lower pressures can be employed, and briquettes made this way are strong. The coal briquettes produced by this technique can be directly used in industry for power generation and other heating.
Conclusion
The composition of Makerwal coal sample indicates that it is sub-bituminous coal containing relatively high value of volatile matter (34.42%), ash content (25.97%) and sulphur (5.78%). The flotation tests showed that it possible to obtain a high-quality clean coal for industrial utilization by decreasing the ash content from 25.97% to 7.80% and sulphur content from 5.78% to 1.37% respectively. Consequently, fixed carbon content has been increased from 35.15% to 55.81% and volatile matter from 34.42% to 35.64% in the final concentrate. The gross calorific value was improved from 5076 Btu/lb in raw coal to 10465 Btu/Ib in final concentrate. The developed process is quite effective for the removals of both ash and sulphur containing mineral matter from coal and producing a high-quality clean coal. The lime-molasses binder combination was appropriate to briquette the clean coal fines. The final clean coal briquette produced was found suitable for industrial applications.
To Know more about Insights in Mining Science & Technology
Click here: https://juniperpublishers.com/index.php
I wasted a lot of money trying to find the right medication for my moms dementia all to no avail until Dr Erayo showed up and eradicated the stigma with the natural roots and herbs i ordered from him , my mom took it for 21days and she was cured from her dementia.
ReplyDeleteGod have use Dr Erayo herbal home to cure my mom, thank you so much Dr Erayo I am so happy. You can email Dr Erayo for help drerayoherbalhome@gmail.com
or whatsapp him on +2348151937428
website---- https://alternativeherbs.weebly.com
Youtube link---- https://www.youtube.com/channel/UCSp2m-_EHnCRQT4gYYTQWtg
FB page---- https://rb.gy/yuofn6
Thank you for giving this content. This is more helpful for eee projects
ReplyDelete