Annals of Reviews and Research - Juniper Publishers
Abstract
Traceability in food supply chain is an issue of growing importance and is directly associated with safety and quality of products and consumers. The emergence of Industry 4.0 and Internet of Things created new opportunities and challenges for companies in the food sector, for ensuring authenticity, safety, and quality. This paper attempts to analyze and highlight the necessity of IoT technologies use in the food supply chain. Moreover, through empirical research, this paper explores the use of enterprise information systems and IoT technologies in a sample of 53 Greek food companies. The results show that, at the moment, companies are still using older and, in many cases, manual systems and they have not moved forward to adopt new technologies such as Qr codes, Wireless Sensor Networks, Blockchain, DNA barcoding etc. However, their traceability systems are connected to the ERP system and provide some basic information, although this information is not shared with partners in the supply chain. The outcomes of our study can help managers to discover the potential of new technologies and enterprise systems on food traceability, along with their challenges and the current state of their implementation. Also, this study can provide the basis for other research efforts that may analyze in more detail factors that hinder the wide adoption of IoT technologies in the food supply chain and also the required workforce skills for the successful implementation and use of these technologies.
Keywords: Traceability; Enterprise Information Systems; IoT; Food safety; Food Supply Chain
Abbreviations: IoT: Internet of Things; RFID: Radio frequency identification; GPS: Global positioning system; WSN: Wireless sensor network; EPC: Electronic product code
Introduction
4. Introduction
Food traceability is a contentious term, since it has a variety of meanings and definitions, based on the supply chain industry sector and the viewpoints of the various stakeholders and users Souali [1]. In general, traceability is known as the ability to track the movement of food product and its ingredients backwards and forward through the supply chain Souali [1]. During the last decade the credibility of the food industry’s quality assurance systems has been seriously questioned due to the emergence of serious food-related incidents, eroding consumer’s trust for food safety and quality. At the same time, the spread of international food trade and economic globalization have caused the expansion of the size and complexity of food supply chains Kher et al. [2]. Food supply chains are complex due to the large number of participants, the different types of record-keeping methods and tools, from modern ERPs to manual systems, the difficulties in predicting supply, the variances in quality and other issues Rejeb et al. [3]. In light of these circumstances, it is essential to set up a reliable traceability system in order to decrease the production and distribution of unsafe and poor-quality food Aung & Chang [4]. For this reason, monitoring is required at every stage of the food supply chain to guarantee the consistency and accuracy of food traceability Houghton et al. [5].
Technologies for food traceability
In the era of Industry 4.0, the transition of businesses from traditional ways of traceability to the application of Internet of Things (IoT) technologies that allow end to end visibility is considered as essential. The goal of IoT is to connect different and disparate smart devices without requiring human intervention Jagtap et al. [6]. According to Ding [7], Song et al. [8] and Mehannaoui [9], technologies used in IoT-based food traceability can be classified in the following categories: 1) identification and monitoring technologies (barcodes, qr codes, radio frequency identification, wireless sensor network etc.), 2) communication technologies (proximity, wireless personal area network, wireless local area network, wireless metropolitan area network and wireless wide area network and 3) data management technologies (big data, cloud computing, data mining, blockchain etc.).
Each of the above-mentioned technologies, with all the advantages and disadvantages mentioned in the literature, can play a significant role in food traceability efforts across the supply chain. For example, barcodes have the advantages of simplicity and lower reader costs, but they have limited data storage capacity, and their use is from specific devices, time consuming and error prone Ayalew et al. [10]. In contrast to conventional one-dimensional barcodes, qr codes can store more data and they can be used by a variety of devices Aho [11]. The use of qr codes is now quite widespread in the food supply chain, not only from companies but also from consumers, who can access information about a product through scanning the qr code with their smartphone Qian et al. [12]. However, a disadvantage of qr code is that once it is generated it cannot be altered Aho [11]. A type of contactless (wireless) data communication technology is radio frequency identification (RFID), which is used to track products using wireless sensor network and global positioning system (GPS) Alfian et al. [13]. The use of RFID improves the accuracy of tracking data and leads to increased supply chain visibility particularly in the food sector Zelbst et al. [14], although it still has high implementation and operation costs and issues such as protection of data privacy and security Nguyen [15].
A modern version of barcode technology is DNA barcoding, which is a labeling method based on DNA sequence, with initial applications in livestock and agriculture, in order to track origin and quality of food products Yu et al. [16]. The use of DNA barcoding can reduce the toxicological and microbiological risks related to consuming food and food-related products Dawan & Ahn [17]. An important limitation of this technology is that requires a reference database of known DNA sequences for comparison: while this database is constantly being updated, it may not contain all possible species, especially those that are rare or have limited commercial use. This may limit the utility of DNA barcoding in identifying specific food products. Processing complex mixtures can be challenging because some food products, like processed foods or dishes with multiple ingredients, may contain DNA from different species. This can make it difficult to accurately identify the product's composition using DNA barcoding Raclariu [18].
A wireless sensor network (WSN) is a network of numerous small sensor nodes that can be mobile or stationary, linked to a central node or gateway and communicate with each other wirelessly Jaiswal & Anand [19]. These sensors can gather a variety of information, including temperature, humidity, location and other environmental factors that have an impact on the quality and safety of food products Mehannaoui & Mouss [9]. WSNs offer a dependable and economical way to keep track and monitor food products from farm to fork, which can improve the transparency, accuracy and accountability of the food supply chain and contribute to the reduction in food waste Mehannaoui [20]. However, WSNs have limited range, making it difficult to monitor food products throughout the entire supply chain and they rely on battery-powered sensors, which may have a short lifespan. Cloud computing is a model of providing on-demand ICT infrastructure and services over the internet, provided through several deployment and service models Nanos [21]. Through cloud computing, food businesses can operate and maintain systems and applications in a more efficient and cost-effective way. Moreover, cloud computing enables participants in the food supply chain to share information and collaborate with business partners, something that will eventually lead to increased visibility across the supply chain Srivastava & Wood [22]. Finally, the use of blockchain in the food supply chain can significantly increase accuracy, efficiency and visibility, through a decentralized series of time-stamped validated and verified blocks that provides immutable data to all parties Devan [23], including consumers, who can trace products back to their sources of origin and verify their authenticity Awan et al. [24].
Background studies
Henson [25] on their research provided an in-depth insight into the implementation of product traceability systems in the Canadian dairy processing sector. They investigated factors that lead to the adoption of product traceability, the nature and level of traceability (measured with variables such as depth, precision and breadth), the costs and benefits associated with this adoption and the constraints in implementing product traceability, according to firm size, product type and markets served. The findings of the research showed that that product traceability is relatively widespread and only a small percentage of survey participants did not use a system for product traceability, however the systems' level of sophistication is not very high. Although they typically allow traceability to the level of at least one day's production, through to retail distribution, and back to single or at least groups of milk producers, the majority of systems were manual rather than computer-based. Also, through the study, three categories of enabling factors for implementing product traceability were identified: market drivers, product recall and legal requirements. The main problems experienced in implementing product traceability were the need for staff training (managerial, production, supervisory and administrative staff), and the need for cooperation with customers and suppliers, as far as the flow of information is concerned. The main expenses associated with implementing a system of product traceability are costs related to auditing, inspection and laboratory testing, procedures that are usually outsourced to external partners.
Preziosi [26] in his dissertation assessed the impact of traceability on the Italian poultry supply chain firms, through an index that measured the level of traceability, based on variables such as breadth, depth, access, technology and precision. Additionally, the survey investigated the benefits of traceability in three main areas: food safety management, potential process improvements and product differentiation. The perceived barriers-challenges of traceability implementation were also examined, such as required changes in existing methods and ICT tools and techniques as well as cost and changes in customer and partner relationship management. The results showed that most companies were in a medium and deep level of traceability. These two groups indicated a significant difference in terms of difficulties in implementing traceability. On the other hand, there is no discernible difference in relation to costs and benefits. In general, firms with a lower level of traceability consider that all factors (benefits, costs, and implementation challenges of traceability) have a greater impact on their operations than firms with deep traceability. Finally, firms with lower traceability demonstrated more significant challenges implementing the European Commission Regulation No. 1169/2011 about food labeling European Commission [27]. Kalogianni [28] conducted a survey in food industry, aiming at the evaluation of traceability systems application and at the analysis of motivating factors for implementing a traceability system, as well as the various problems that arise and the proposed solutions.
According to the results, almost half of the companies used both manual (handwritten) and electronic (computer-based) systems. Also, it was found that firms did not keep traceability information about each product, but for the batch of products that were produced every day. As far as the main drivers for implementation of traceability systems are concerned, the survey indicated the need for accurate recalls and the pressure from competitors and partners in the supply chain, especially from other countries. The main problems that arise when implementing traceability systems is the reaction time in the event of a recall, the response time and transparency in supplier information, the retention time of manual traceability and the traceability of bulk products. Tools such as electronic traceability application system, electronic product code (EPC) and RFID tags with sensors, seem to be first in preferences of the food companies examined. Also, most firms suggested that legislation about traceability should be more specific and strict. Finally, it should be noted that most businesses are quite hesitant to send products with more information on the shelf, because they are concerned about confidentiality of their business data.
Based on all the above studies, the aim of this paper is to explore and analyze the use of enterprise systems and technologies for traceability in food supply chain, through an empirical study in Greek companies. The main research questions are the following: RQ1: Which are the enterprise systems and IoT technologies used for traceability by Greek food companies? RQ2: How accurate and deep is the traceability system in capturing and tracking multiple attributes of products? RQ3: What is the level of accessibility of the traceability system for different stakeholders within the supply chain? RQ4: How deep is the traceability system in terms of allowing for trace-back and trace-forward analysis in case of quality issues or recalls?
Materials and Methods
The research method chosen was a quantitative research through an online survey in food companies in northern Greece. The population of the survey was companies of the food industry sector that are based in northern Greece and are either food producers or wholesalers. In order to locate these companies, an initial research was made in the website infood.gr, which is a complete guide for food and beverage suppliers in Greece. Moreover, research was performed in resources such as the Association of Greek Food Producing Companies, in government portals such as enterprisegreece.gov.gr and finally in Google and LinkedIn. An initial list of 160 companies was created. Every company was contacted firstly by phone, informing managers about the aim and scope of the research and then an email was sent, containing the link to the electronic questionnaire and instructions for the survey. A total number of 53 companies participated in the survey, thus forming the sample of our research. Responses were collected through a Google form. After the end of the survey, data was coded and analyzed with IBM SPSS Statistics 25.0.
Results
Initially, the participants were asked to answer about the traceability system applied in their company (handwritten, electronic or both). Those who answered electronic or both were then asked if the system is connected to an ERP (Enterprise Resource Planning) system as well as which technology they use to record, track, and identify products. According to the results presented at Table 1, most of the companies replied that they use both manual and electronic system, while 35,85% use exclusively electronic traceability system. In all companies that are using an electronic traceability system, this system is connected to an ERP (see Table 2). Missing values refer to the companies that apply manual traceability system. Then, the respondents were asked to answer about the type of technology (Barcode, Qr code, RFID, DNA barcoding, Wireless Sensor Networks and Blockchain) used in their company in order to record, track and identify products. The participants could select either one or more than one answer, e.g. barcode, barcode and qr code, DNA barcoding and Blockchain and Wireless Sensor Networks etc. None of the companies uses the technology of blockchain and wireless sensor networks, while the vast percentage of companies (79,50%) uses barcode. Some companies (12,80%) use barcode and Qr code, while a limited number of companies (7,70) uses barcode and Qr code and Wireless Sensor Networks (Table 3).
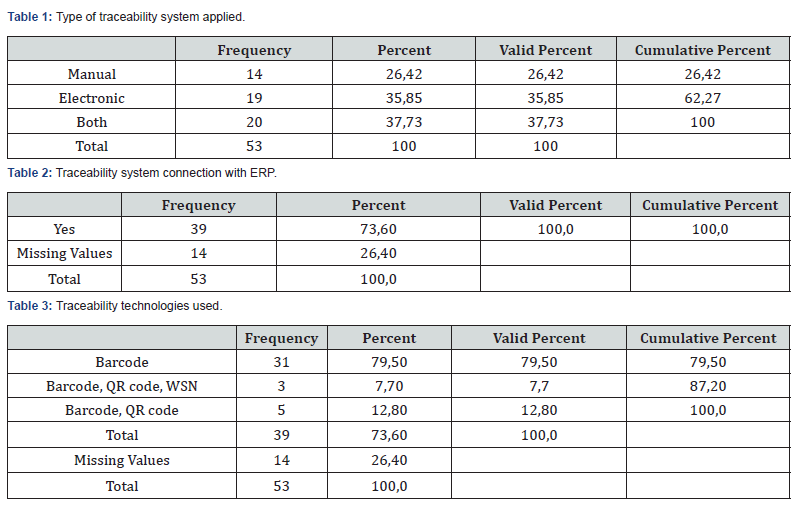
To determine how accurate and comprehensive is the applied traceability system, companies were asked how they define the batch, what information their traceability system provides them and which data is captured when a raw material or a product arrives at their premises. As presented at Table 4, half of the respondents (50,90%) define the batch as “the set of products produced under the same conditions”, while a percentage of 43,40% consider it as “the total production in one day”. Concerning the type of information provided by a traceability system, 52,80% of the companies can find information on a specific batch, while 43,40% can find information on both a specific batch and a specific product (Table 5). Regarding the type of data collected when a raw material or a product arrives at the company, respondents had to choose between the date and time of entry, supplier, origin, quantity, packaging details, temperature and storage conditions, quality and safety certifications and a combination of them. As shown in Table 6, the majority of companies (35,80%) collect all the reported data, while 32,10% of the sample collects only the date and time of entry, supplier details, origin, quantity, temperature and storage conditions, quality and safety certifications.
In the following section of our questionnaire, the level of accessibility of the traceability system for different stakeholders within the supply chain was investigated. Firstly, companies were asked if they use a common online database to share real-time information in the event of a food safety threat. According to the results in Table 7, most of the companies (41,50%) do not use such a system, while a percentage of 32,10% maintains a common online database to share real time information with the competent public authorities in the event of a food safety threat. Then, the participants were asked if their companies use a common traceability system with their suppliers in order to exchange information. As presented at Table 8, the vast majority of companies (84,90%) do not use such a system. Concerning the depth of the traceability system, in terms of allowing for trace-back and trace-forward analysis in case of quality issues or recalls, the results showed that 94,30% of the companies trace the origin of raw materials (Table 9). At the same time, and according to Table 10, half of the companies record all data until the arrival of the goods at the retailer.

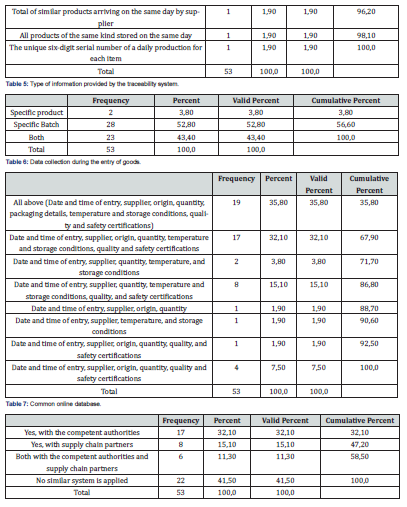
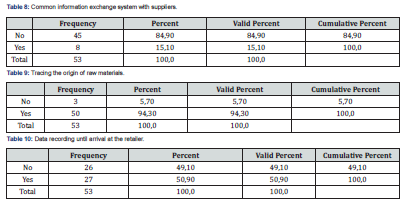
Discussion
As far as the first research question (RQ1) is concerned, about the systems and technologies used for food products traceability, most companies apply a combination of manual and electronic system, connected in most of the cases with an ERP system. The technologies used for traceability are mainly barcodes and qr codes and companies have not adopted yet current IoT technologies, such as RFID, Wireless Sensor Networks, Blockchain, DNA barcoding etc. With the second research question (RQ2) we tried to identify the accuracy and the depth-range of the traceability system in identifying and tracking individual products or products batches throughout the supply chain. As far as the accuracy is concerned, more than half of the companies define the batch as the set of products produced under the same conditions. This type of traceability system is generally more accurate in ensuring that products with identical production conditions are correctly identified and tracked. Also, it helps maintain consistency in quality and safety for products that undergo similar processes. Regarding the information provided by the traceability system, companies track information both on batch level and a specific product. As far as the depth (range) of the traceability system is concerned, the majority of food companies record the data that is required by the European Commission regulation No 668/2014 European Commission [29], which refers to the supplier, the origin and the quantity. A small percentage of businesses do not record either quantity or origin. Furthermore, many companies collect additional data beyond the legislative prerequisites, such as date and time of entry, packaging details, temperature and storage conditions, quality, and safety certifications.
The third research question (RQ3) regarded the level of accessibility of the traceability system for different participants in the food supply chain. In the majority of companies there is no use of a common online database with supply chain partners, while a respectful percentage of companies use a common database to share information with competent public authorities. Similarly, most of the companies do not have a common traceability system to exchange information with suppliers. Finally, in the case of tracing back or tracing forward in order to examine the depth of traceability system, which is our fourth research question (RQ4), in most companies the traceability system allows them to track the origin of raw materials (trace-back). It should be noted though, that half of the companies in our sample can record data up to the arrival of the product at the retailer, while the other half do not (trace-forward).
Conclusion
From the literature review it is evident that traceability in the food supply chain is a very important aspect and of growing importance. Technological developments are rapid and continuous, offering multiple and innovative solutions for industry and stakeholders that enhance the quality and safety of the final product. IoT technologies is one of the most significant and recent developments in the field of IT. A main advantage recorded in the literature concerning the importance of using IoT technologies, is the empowerment of stakeholders by enabling them to control and manage connected equipment and by monitoring food production flows in real time. In addition, the use of IoT and of proper enterprise systems enables the quick identification of quality issues and allows more efficient and accurate data collection and analysis, leading to improved decision-making and enhanced operational efficiency. However, some concerns regarding the adoption of IoT technologies are identified, such as connectivity issues, data security, economic sustainability of all stakeholders and willingness of consumers to pay more for food produced with greater transparency.
The empirical research conducted in order to identify the technologies used by Greek food companies and the capabilities of their traceability systems, showed that the use of IoT technologies is not yet widespread. Companies still use older technologies, such as barcodes, together with manual and electronic systems. The traceability system of most companies is quite accurate in identifying batches of products as they define the batch as the total of products produced under the same conditions. In addition, the traceability system applied by companies is quite detailed in capturing and tracking multiple attributes of products as, apart from the legal requirements, it also records additional data at the entry of a product. However, most companies do not have a common online real-time information database, both with the competent authorities and with stakeholders, nor a system for exchanging information with suppliers. As far as the depth of the applied traceability system is concerned, most companies have the ability to track the origin of raw materials as well as record all data until the product arrives at the retailer.
The limitations of our research mainly refer to the sample: a larger number of companies or a sample consisting of companies from all over the country might have produced different results. However, the outcomes of our study can still be useful and applicable, both for practitioners-managers in the food supply chain and for academics-researchers. Further research in the area may include analysis of the factors that hinder the wide adoption of IoT technologies in the food supply chain and on the skills of the workforce for the successful implementation and use of these technologies.
To Know More About Annals of Reviews and Research Please click on:
https://juniperpublishers.com/arr/index.php
For more Open Access Journals in Juniper Publishers please click on:
https://juniperpublishers.com/index.php
No comments:
Post a Comment