Mining Science & Technology - Juniper Publishers
Abstract
Magnetizing reduction is an important pre-treatment process used for low-grade iron ores which are difficult to upgrade by conventional beneficiation techniques. In present study, magnetizing reduction of a low-grade iron ore has been carried out followed by magnetic separation of iron minerals to produce iron concentrate. A potential process has been developed for magnetizing reduction of hematite into magnetite with domestic lignite coal. The experiments were carried out in Muffle furnace under controlled temperature conditions. The main process variables such as particle size of ore, ore to coal consumption ratio, reduction temperature and retention time were investigated to determine the extent of magnetizing reduction. In second step, reduced iron ore was subjected to low intensity magnetic separation to recover iron values in the magnetic concentrate. A single-factor variation method was applied in order to get the optimum conditions of the process. The results of bench scale experimental study showed that the maximum grade and recovery of iron concentrate was achieved at ore size of 90-95% minus 200 mesh, ore to coal consumption ratio of 1: 0.25, the reduction temperature of 700°C and the retention time of about 60 minutes. The ore containing 33.95% Fe was upgraded to a concentrate assaying 64.13% Fe with 83.70% recovery. The iron concentrate produced meets the specifications of metallurgical grade and is suitable for use as a feed for blast furnace and other direct reduction methods.
Keywords: Low-grade iron ore; Beneficiation; Magnetizing reduction; Low intensity magnetic separation; Iron concentrate; Hematite; Magnetite; Metallurgical grade; Recovery
Introduction
Conventionally iron and steel is produced by the reduction of high-grade iron ores in a blast furnace. About 80% of the world’s iron making is achieved through the blast furnace process and rest by different direct reduction (DR) processes. The role of high-quality iron ore and concentrate as a raw material is very critical to get the best quality iron and steel [1]. The high-grade iron ores or concentrate should contain at least 60% iron (Fe) content with maximum up to 7% silica (SiO2) content [2]. The product of blast furnace is a pig iron which is then converted into steel by various techniques [3]. The quality of raw materials used in blast furnace plays an important role in steelmaking process.
The iron ores available at different areas of Pakistan are generally low-grade with high silica content. These ores as such cannot be utilized to produce iron and steel by conventional blast furnace technique or DRI processes. The first step in iron making involves the separation of iron minerals from low-grade iron ores. There are three basic methods for separation of iron minerals i.e., magnetic separation, froth flotation and gravity concentration [4]. The iron concentrate produced by any processing method is used for producing iron metal either by blast furnace or direct reduction methods [5]. The fine iron concentrate is to be palletized or sintered for both routes [6].
Magnetic separation is most used to separate natural magnetic iron ore (magnetite) from a variety of less magnetic or nonmagnetic material [7]. Magnetizing reduction is one of the most effective unit operations in the treatment of low-grade iron ores specially those which are poorly responsive to conventional beneficiation techniques such as froth flotation, gravity separation and magnetic separation [8,9]. It involves the conversion of feebly magnetic iron minerals in the ore to the strongly magnetic form by subjecting the ore to a reducing atmosphere at elevated temperatures. The resulting artificial magnetite is strongly magnetic and can be separated from the non-magnetic gangue by low-intensity magnetic separation. Many weakly magnetic minerals can be converted to more strongly magnetic compounds by magnetizing reduction processes [10-12].
Geological Survey of Pakistan (GSP) during regional survey in 1989 discovered iron ore deposits near Chiniot town and adjoining areas such as Rajoa, Chak Jhumra, Wad Syedan, Ghutti Syedan, Shaheen Abad, Sargodha and Sangla Hills etc. Subsequently, the Punjab Mineral Development Corporation (PUNJMIN) carried out detailed exploration in year 2005 to 2007. As a result of exploration work, anomalous zones containing iron ore and other associated metallic minerals have been confirmed in Chiniot with strong indications in Rajoa. The other metallic mineral resources including copper, gold, nickel, cobalt etc. are also found in the underlying sulphide zone associated with the iron ore. Around 150 million tons of good quality iron ore reserves had been identified in Chiniot. The field survey based on the cores recovered from several drill holes of the ore body has shown that the ore occurs in bands ranging from one meter to several meters in thickness. The Chiniot iron ore is predominantly oxide ore containing variable amount of hematite and magnetite as principal iron bearing minerals. The ore is massive, low to medium grade containing as low as 30 Fe2O3 to as high as 70 Fe2O3. The resources are buried under alluvium, aquifers and hosted in the subsurface volcanogenic rocks [13].
With ever rising steel prices, the local manufacturing of steel based on indigenous reserves of iron-ore is critical. The main problems in utilization of indigenous iron ore is up-gradation and beneficiation of available resources. Development of domestic technologies for utilization of indigenous iron ore will not only reduce the dependence of steel production on imported raw material, but it will also result in lowering the steel price. Present beneficiation studies are oriented towards exploring the possibilities of upgrading Chiniot iron ore to produce iron concentrate for utilization as a feed in conventional blast furnace or direct reduction method to produce iron and steel.
Materials and Methods
Sample Preparation
The core samples of seven drill holes of Chiniot iron ore weighing about 40kg were received for beneficiation studies. The drill cores were crushed in laboratory jaw crusher (set at 20mm) followed by roll crusher (set at 5mm) for size reduction. Riffling technique of sampling was used to prepare the head sample for chemical analysis. The head sample was pulverized to 100% minus 200 mesh (74µm) in disc pulverizer (Denver, USA). The crushed ore was split into 1kg samples and kept in plastic zipper bags for R& D work. These ore samples were ground in rod mill for magnetizing reduction and magnetic separation tests.
Chemical analysis of ore
The chemical analysis of head sample of iron ore originating from Chiniot area was carried out by standard wet analytical methods and atomic absorption spectrometer. Ore was fused with sodium carbonate and sample solution was made in dilute HCl. Silica, alumina, and sulphur were determined gravimetrically while iron was determined by oxidation reduction titration. Calcium and magnesium were determined by complexometric titration using standard solution of EDTA. Sodium and potassium were determined by flame photometer (PFP7, Jenway Limited, England). Loss on ignition (LOI) was determined at 1000oC. The complete chemical analysis of head sample of Chiniot iron ore is shown in Table 1.
Magnetizing Reduction Tests
Magnetizing reduction tests were carried out on ground ore using locally available lignite to sub-bituminous coal used as reducing agent. The pulverized coal sample used has 2.45% moisture, 37.79% ash content, 35.20% fixed carbon, 24.56% volatile matter, 5.86% sulphur and its gross calorific value of coal was 6150 Btu/lb. Known weight and sizes of ground ore and coal were mixed in different composition. These were placed in porcelain crucibles (100ml capacity) and covered with lid. These were heated by gradually by raising the temperature with increment of 100°C per 30 min in electric (muffle) furnace to desired temperature and then maintaining it for magnetizing reduction of hematite into magnetite. The crucibles were removed after keeping them at different temperature for different time interval. Runs were conducted on 50g ore charged. The ore to coal ratio was studied from 1: 0.1 to 1: 0.30, the reduction temperature was ranged from 500 to 800°C, the residence time was varied between 30 min to 120 min and the particle size of ore was varied from 90-95% passing 100 mesh to 250 mesh.
Magnetic Separation Tests
The reduced ore (feed) was subjected to wet low intensity rotary drum magnetic separator (Sala, Italy) having permanent magnets for separation of magnetic minerals form associated gangue minerals. The drum dimensions were 200 mm dia × 100 mm width. The intensity of magnetic field (strength) was set at 1000 gauss. Tests were conducted at feed rate of 10-15 kg/hr, wash water flow rate of 20-25 l/hr and number of operations (passes) 2. The magnetic (concentrate) and non- magnetic (tailings) portions were collected separately, dewatered and oven dried. The dried concentrate and tailings were weighed and chemically analyzed for total iron content. The results of magnetic separation tests are given in Table 2. The flowsheet developed for the process is given in Figure 1. The images of the crushed sample, ground head sample, ground lignite coal and reduced magnetic concentrate are shown in Figure 2.
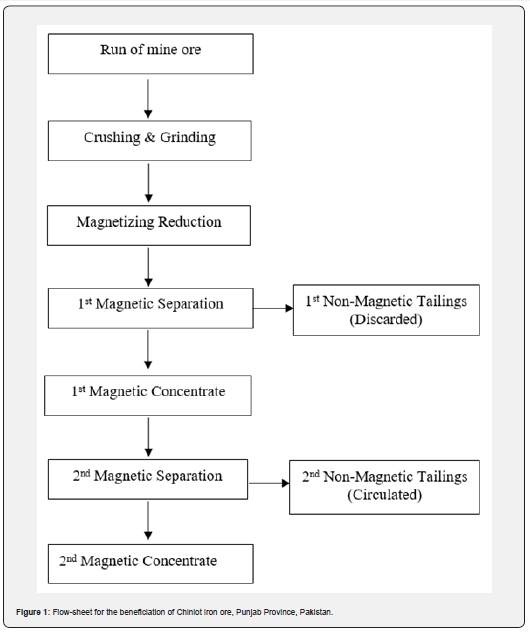
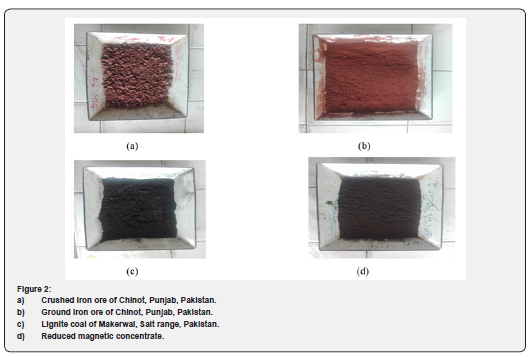
Results and Discussion
Chemical analysis
The chemical analysis of head sample (Table 1) indicates that ore contains 33.95% total Fe. The main impurity is silica being 36.25% which is more than the permissible limit required for iron and steel production. The level of other impurities is not very high except sodium oxide and potassium oxide. These impurities are present due to the occurrence of cerecite and feldspar in the ore. The iron mineralization varies from massive over 70% Fe2O3 through medium 50% Fe2O3 to low grade 30% Fe2O3. The iron minerals occur as hematite and magnetite. The hematite to magnetite ratio varied from 1. 3:1 to 2.0:1. The ore is hard, tough and compact. As hematite is a weekly paramagnetic mineral, while the other minerals present in the ore are diamagnetic in nature. It was decided, in this perspective, to convert hematite into magnetite followed by low intensity magnetic separation technique which has the potential to recover the iron values and reduce the siliceous gangue minerals effectively [14].
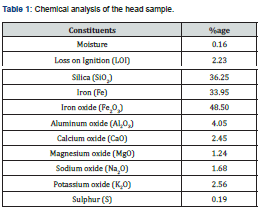
Effect of particle size of ore
The particle sizes worked at were almost 90-95% passing 100 mesh (150µm), 150 mesh (100µm), 200 mesh (75µm) and 250 mesh (65µm) for magnetizing reduction study keeping other factors constant. The results of beneficiation tests (Figure 3) showed that although some up-gradation has been affected at coarse size. However, the concentrates were high in silica content showing thereby that it is locked within iron oxide particles. It was thought essential to grind the ores to finer size. It was observed that the samples ground to 90-95% passing 200 mesh responded most favorably to magnetic separation. The magnetizing reduction followed by magnetic separation results showed that as the particle size of feed was reduced from 90-95% passing 100 mesh through 150 mesh to 200 mesh, the grade was improved gradually from 52.45% Fe through 58.90% Fe to 61.05% Fe with slight decrease in recovery of total iron content of concentrate from 87.12% through 85.03% to 84.72%. However, after that both grade (58.23%) and recovery (80.31%) were dropped sharply probably due to finer particle size of ore.
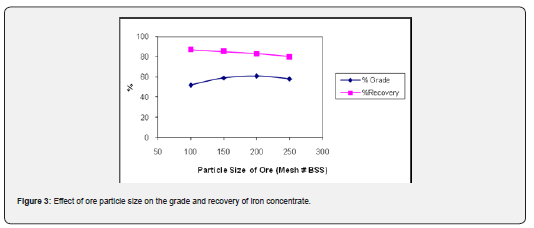
Effect of reduction temperature
Temperature has a significant effect on magnetizing reduction process. It plays an important role in the phase change of hematite and limonite during magnetizing reduction [15]. The iron ore samples of 90-95% passing 200 mesh size were subjected to magnetizing reduction with excess of coal (30%) at 500°C, 600°C, 700°C and 800°C for 60 min to study the effect temperature on the magnetizing reduction of iron ore. The reduced samples were separated, and magnetic fractions were subjected to chemical analysis to determine the iron content. The results obtained are shown in Figure 4. It is clear from this figure that iron grade and recovery in the magnetic fraction exhibits a gradual increase with rise in reduction temperature and reaches at maximum value 62.31% Fe with 82.75% recovery at the onset of reduction temperature of 700°C and then slowly declines. It is since as the temperature is raised between 200 to 700°C the carbon in the form of coal burns to produce carbon monoxide.
2 C(s) + O2(g) → 2 CO(g)
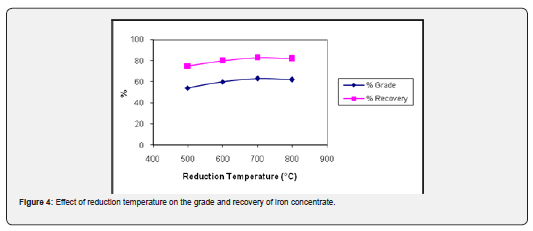
The hot carbon monoxide is the reducing agent for the iron ore and reacts with the hematite iron oxide Fe2O3 (III) to produce magnetite iron oxide Fe3O4 (II) and carbon dioxide.
3 Fe2O3(s) + CO(g) → 2 Fe3O4(s) + CO2(g)
The hot carbon dioxide formed in this process is re-reduced to carbon monoxide by further reaction with the coal.
C(s) + CO2(g) → 2 CO (g)
As the temperature is further increased beyond 700°C, most of the coal is consumed away and some of freshly converted magnetite present on the surface is re-oxidized to hematite by air which lowers the recovery rate during magnetic separation [16].
Effect of reduction time
The effect of reduction time was investigated by varying it from 15 to 75 minutes with increment of 15 min and keeping other parameters constant at feed size of 90-95% passing 200 mesh size, the reduction temperature of 700°C and ore to coal ratio of 1: 0.30. It is obvious from the result (Figure 5) that iron grade and recovery in the magnetic fraction increases gradually in the beginning and then represents a sharp increase (63.45% Fe with 82.93%) at the onset of reduction time of 60min and then decreases with increase in reduction time. It is observed that when the reduction time was extended from 60min, the magnetic properties of the reduced ore were decreased (Figure 2). The prolonged reduction time results in excessive reduction and waste of energy resources. Also, when the reduction time is less than 60min, insufficient reduction occurs leading to lower metallurgical results [17].
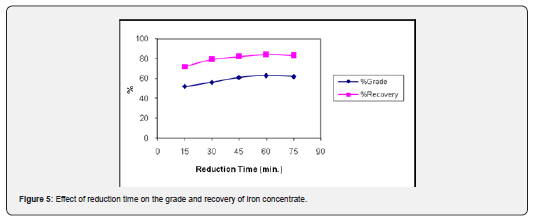
Effect of coal consumption ratio
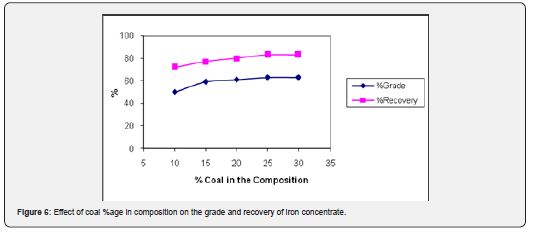
The effect of coal as reducing agent on the reduction of hematite to magnetite was investigated by varying the ratio of ore to coal from 1: 0.10 to 1: 0.30 in the charge at a temperature of 700°C for 60 min using the particle size of 90-95% minus 200 mesh size. The coal carbon burns as the temperature is increased and reducing gases such as carbon monoxide are formed that initiate the reduction of hematite into magnetite. As a result, this reaction, conversion of hematite into magnetite takes place [18,19]. The results obtained (Figure 6) show that the metallurgical performance (grade and recovery) of magnetizing reduction is improved and reaches its highest value of 64.13% Fe with 83.70% recovery as the ratio of coal in the ore was increased up to 1: 0.25 in the charge. Further increase seems to be insignificant as it does not improve the results.
Effect of Magnetic Separation
Low-intensity magnetic separators use magnetic fields between 1,000 and 3,000 gausses [20]. Low-intensity magnetic separation techniques are normally used on magnetite ore as an inexpensive and effective separation method. This method is used to capture only highly magnetic material, such as magnetite. High-intensity separators employ fields as strong as 20,000 gausses. This method is used to separate weakly magnetic iron minerals, such as hematite, ilmenite, rutile, siderite, chromite, wolframite, pyrrhotite, monazite from non-magnetic or less magnetic gangue material [21-25]. The preliminary direct low-intensity magnetic separation tests showed that ore contain mainly hematite as iron bearing mineral as only 25 to 35% of total iron (Fe) corresponding to magnetite was recovered by low-intensity magnetic separation. Between 30 to 35% of all the iron units being beneficiated are lost to tailings because hematite is only weakly magnetic.
The optimum conditions of magnetizing reduction parameters (Table 2) depict that when the crude ore grade is 33.95% Fe, the mass percent of pulverized coal as reducing agent is 25%, reduction temperature is 700℃, reduction time is 60 min and particle size is 90-95% passing 200 mesh # (0.074mm). The iron concentrate can be got after a low-intensity magnetic separation, whose grade is 64.13% Fe and recovery is 83.70%.
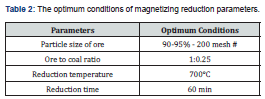
Metallurgical balance Calculation
The metallurgical balance (Table 3) shows that Chinot iron ore is amenable to beneficiation using low-intensity magnetic separation after magnetizing reduction technique. The magnetizing reduction trials of iron ore followed by magnetic separation has indicated that the ore has been concentrated to 64.13% Fe grade with 83.70% recovery starting from a crude ore assaying 33.95% Fe. The silica content is greatly affected by the magnetizing reduction treatment where it decreases from 36.25% in the ore to 4.38% in the magnetic portion. Magnetizing-reduction has been found an efficient technique for the recovery of values from this ore with acceptable recovery. The developed process is low energy consuming, cost effective and convenient.
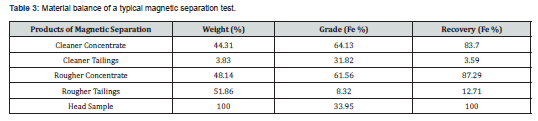
Final concentrate analysis
The chemical analysis of final concentrate (Table 4) reveals that after beneficiation, iron content (Fe) has been increased significantly from 33.95% to 64.13% with decrease in amount of silica (SiO2) from 36.25% to 4.38%. The prepared iron concentrate having iron and silica in this range is considered suitable for the preparation of iron and steel by Blast Furnace and alternative iron making processes such as SL/RN, Krupp-Renn, Midrex, Corex, Hyl, Romelt, Hismelt, Ausmelt, Dios etc. [26]. There is a quite variation in selection of feed for different processes. The reducing agents may be gas or solid or both fuels. The charge may be lumps, screen size, fines, pellets, sinter, agglomerate or briquettes. The quality of iron ore or concentrate is key parameter in the selection of process. Some rotary kiln processes such as (Krupp-Renn/ SL/RN) can use lower grade iron ores (Fe 50%) while other process require high grade iron ore having more than 65% Fe content such as Midrex process. The product of DR processes is sponge iron which is converted into steel [27].
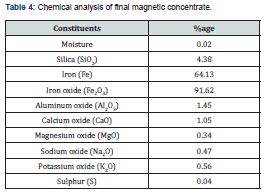
The quality of high-grade iron ore or concentrate made from low grade ore has a significant effect on the efficiency and economy of blast furnace. The various impurities present in iron ore in the forms of silica, alumina, alkalis, phosphorus and sulphur behave differently during smelting and adversely affects the performance and economy of blast furnaces. The presence of phosphorus and sulphur increases surface cracking during steel processing. The acceptable levels of phosphorous (P) vary from 0.08 to 0.14%, while sulphur (S) is up to 0.06% in hot metal. High alkali (Na2O & K2O) contents lower the mechanical strength of coke and sinter, imbalance the furnace operation, reduce the furnace productivity and damage the lining. The desired levels of alkalis are 0.4% of hot metal. The increase in silica (SiO2) content leads to the generation of more siliceous slag with high viscosity, consumes more limestone or dolomite. The desired level of silicon (Si) in the steel is 0.6%. High alumina (Al2O3) decreases the fluidity of slag, and more coke is required to increase the fluidity. It has been reported that reduction of the alumina content in iron ore by 1% improves blast furnace performance by 3%, reduces reduction degradation index (RDI) by 6 points, lowers the coke rate by 14 kg per ton of hot metal and increases sinter productivity by 10-15%. The high iron (Fe) content and low impurities contents in iron ore are highly desired in the blast furnace operations and economy. Different steel plants have varied quality requirements based on the techniques and process adopted. Specifications of a typical iron ores required by steel plants for iron making are as Fe 60-67%, SiO2 1-6%, and Al2O3 3- 4%. The values of these constituents in the iron concentrate prepared from Chinot iron ore lies well within the acceptable limits [28,29].
Conclusion
The results of the experimental study showed that the quality of Chiniot iron ores can be greatly improved by subjecting to magnetizing reduction followed by magnetic separation technique. A great deal of impurities is removed, and the iron content is significantly increased. The ore concentrate obtained is high-grade material suitable for direct use as a feed to produce iron and steel in number of processes. The results reported show that it is possible to upgrade low grade iron ore of Chiniot area by magnetizing reduction followed by low intensity dry magnetic separation technique to produce iron concentrates of metallurgical grade with acceptable recovery. The SiO2 content was reduced remarkably from 36.25% to 4.38%. The iron contents were upgraded significantly from 33.95% to 64.13% at recovery of 83.70%. The final concentrate produced meets all the specifications of the metallurgical grade iron concentrate and can be directly used to produce iron and steel after palletizing. The advantage of this technique is that it is easy to operate, less expensive and environment friendly.
To Know more about Mining Science & Technology
Click here: https://juniperpublishers.com/index.php
No comments:
Post a Comment