Civil Engineering Research Journal - Juniper Publishers
Introduction
Morocco, with estimated reserves of 93 billion tons [1], is increasingly looking at oil shales as an alternative energy source. Many studies have concentrated on oil shales located in Timahdit and Tarfaya, because of their high proportion of organic matter [2]. Most of the studies focused either on the yield and the quality of the oils obtained by conventional pyrolysis or on the characterization of these oils by different physical and chemical techniques [3-6]. In addition, oil shales have a certain potential for the production of several synthetic products such as cement, sulfur, ammonia, adsorbent carbons, carbon fibers and other chemicals [7-9]. In this work, we explore the possibility of transforming the oil shales to materials with high added value. More specifically, we aim at demonstrating that the organic fraction of the oil shales could be used as precursor of low-cost carbon fibers or graphitizable carbon, after appropriate chemical treatments resulting in a “maturation” of this organic phase.
Activated Carbon Fibers from Moroccan Oil Shales
Preparation of the precursor of carbon fibers (pitches)
The oil shale used in this work was from the Tarfaya deposit located in the South of Morocco. This deposit consists of several layers that are subdivided in sub-layers, each having a different amount of organic matter. The samples were obtained from the so-called R3 sub-layer characterized by its high content of organic matter [10-12]. Its chemical composition is given in (Table 1).

Preparation of the raw material
The carbonate-free oil shale was obtained by dissolution of carbonates with HCl [13,14]. The powdered R3 shale (20 g, grain size 0.063-0.08 mm) and 80 mL of concentrated HCl (7 M) were introduced in an Erlenmeyer. The mixture was then subjected to magnetic stirring for 4 h. The formed CO2 was trapped by bubbling in a solution of barium hydroxide. After filtration, the solid residue (referred to as RH) was washed carefully with distilled water, dried at 100 °C and stocked in a sealed plastic bag.
Procedures
Supercritical extraction of RH (10 g) with toluene was conducted in a 120 mL stainless steel autoclave equipped with a pressure gauge and heated in a tubular furnace whose temperature, as well as the heating rate, was controlled (Figure 1). The temperature of extraction was 390 °C with a heating rate of 16 °C·min-1 [15]. The maximum pressure reached during this treatment of 120 min was 5.3 MPa and 7.5 MPa for a volume of toluene of 50 mL and 70 mL respectively, beyond the critical point of toluene (320 °C, 4.2 MPa), After being cooled to room temperature, the mixture was extracted in a Soxhlet apparatus with chloroform for 12 h. The solvent was removed under reduced pressure, and then the organic material was dried for 12 h at 40 °C and weighed. The recovered oil was treated with n-hexane in a 1/10 oil to solvent mass ratio [16]. After stirring for 12 h, the two fractions, soluble (maltenes) and insoluble (asphaltenes), were separated by filtration through Whatman paper, and then dried for 12 h at 40 °C and 80 °C respectively. The maltenes were fractionated in a silica gel column (70-230 mesh, 1 m long and 1.5 cm diameter). Elution of paraffinic, aromatic and polar compounds was performed with hexane, toluene and methanol, respectively [16]. The high-molecular fraction (asphaltenes) constitutes the pitch.

Preparation of carbon fibers
The black, solid precursor is soluble in toluene and its softening point is about 120 °C. It was melted at 150 °C in a laboratory-made spinning device with a single spinneret, equipped with a filter to remove solid particles from the melt. After extrusion and mechanical stretching, the fiber was thermoset by oxidation in dry air by being slowly heated at atmospheric pressure to the temperature in the range 60-280 °C. The thermoset fibers were pyrolyzed under nitrogen flow. The temperature was progressively raised up to 950 °C with a rate of 5 °C·min-1.
Activation of the carbon fibers
The pyrolyzed carbon fibers were activated with phosphoric acid [17] at different temperatures. The samples were impregnated in H3PO4 (10 %) for 1 h and then dried in air at 120 °C for 2 h. The activation reactions were performed in a thermolyne silica electric oven with a temperature control device linked to a thermocouple. The steam generator was placed at the entrance of the reactor. The activation was carried out either under nitrogen or under steam flow. In both cases, the carbon fibers were placed in the reactor and the temperature was progressively raised at a rate of 5 °C·min-1 up to 500 °C, 700 °C and 850 °C, under nitrogen flow, and then the system was set at the maximum temperature that was maintained for 1 h. The first series (FHN) was treated under nitrogen atmosphere and the second series (FHV) under water vapor (Table 2). At the end of the activation, the oven was cooled to ambient, and then the activated carbon fibers were retrieved and boiled for 2 h in distilled water, then washed, dried and retained for subsequent analyses.

Characterization of the activated carbon fibers
These activated carbon fibers are essentially microporous. The adsorption isotherm is of type I of the BDDT classification [18] and the t-plot [19], which compares the nitrogen adsorption isotherm obtained for the studied porous solid to a reference isotherm determined on a nonporous solid, presents a negative deviation from straight line, which is characteristic of micropores. This observation is confirmed by the B hysteresis characteristic of pores, according to the de Boer classification [20]. The surface area and the pore diameter calculated by the BET method [21] are given in (Table 3).

Scanning electron microscopy (SEM)
Samples FHN850 and FHV850 were analyzed by SEM. The micrographs in (Figure 2) show little pores at the outer surface of the two activated fibers, but micrographs of cross section surfaces present a great difference between the samples. They reveal that activation under steam flow produced fibers with a homogeneous repartition of porosity. In the case of activation under nitrogen, the experimental conditions used were insufficient to create a large porosity, which is observed only at the surface of the fiber.
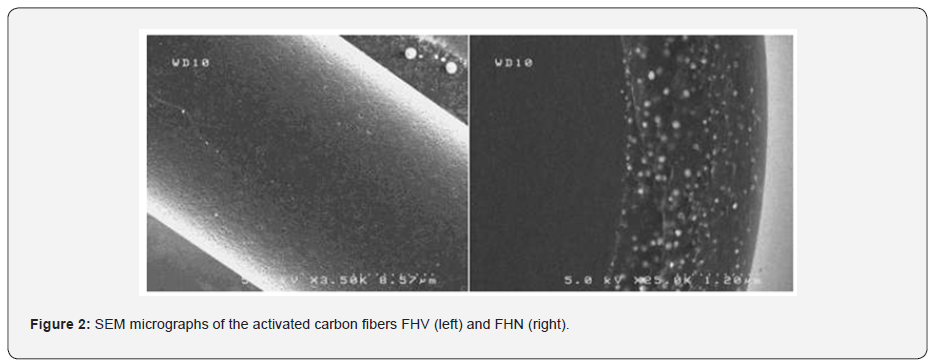
New Graphitizable Carbon Obtained from Moroccan Oil Shales
Our objective was to study the possibility to produce new pitches by using the insoluble fraction resulting from the separation by hexane of the oils recovered from Moroccan oil shales. The evolution of the degree of graphitization of carbons resulting from the pyrolysis of oil shale pitches in the temperature range 1100-2800 °C was studied by Raman spectroscopy in order to determine the operating conditions that were likely to give a pitch leading to a graphitizable carbon [22,23]. The pitches obtained under different conditions of treatment by supercritical extraction were subjected to pyrolysis at 1100 °C and subsequent heat treatments between 1400 and 2800 °C, in order to obtained carbon materials with different degrees of graphitization. After each treatment, the residue was characterized by Raman spectroscopy (Figure 3). The results obtained shows that the degree of graphitization was strongly dependent on the composition of the pitch. Interestingly, it was found that the organization of carbon began at relatively low temperatures. Thus, beyond 1400 °C, a marked structural evolution occurred, leading to a more or less ordered material, according to the composition of the pitch and its preparation conditions. Moreover, phenol is a good extraction solvent under the operating conditions used, leading to carbon pitches with a high graphitization aptitude. The pitches treated at 2800 °C were also analyzed by SEM (Figure 4). These images largely confirm the results of analysis by Raman. Indeed, the pitches treated at 2800°C have a rather unique structure and surprising. This structure is similar to a laminated structure with the appearance of regular hexagons, which is characteristic of a good carbon structural organization.


Conclusion
The present work is part of a more general program for the exploitation of natural resources, and more particularly the Moroccan oil shale deposit of Tarfaya. We have presented a new process using supercritical extraction to produce activated carbon fibers or graphitizable carbon. The fibers exhibit low mechanical properties owing to the isotropic character of the precursor and the absence of mechanical stretching during pyrolysis. The activation of the fibers with phosphoric acid at 850 °C yields a carbon fiber with a specific area of 800 m2·g-1. These fibers can be used as adsorbent or filter in environmental applications. We also prepared new pitches starting from the extraction of Moroccan oil shales. Aptitude for graphitization of carbon resulting from their pyrolysis at increasing temperatures was studied by Raman spectrometry. The degree of graphitization was strongly dependent on the composition of the pitch. Interestingly, it was found that the organization of carbon began at relatively low temperatures. Thus, beyond 1400 °C, a marked structural evolution occurred, leading to a more or less ordered material, according to the composition of the pitch and its preparation conditions.
To Know more about Civil Engineering Research Journal
Click here: https://juniperpublishers.com/index.php
No comments:
Post a Comment