Academic Journal of Polymer Science - Juniper Publishers
Abstract
The dynamic rheological behavior of a
polymethylvinylsiloxane (PMVS)/ low density polyethylene (LDPE) blending
melts at 150,180 and 210 ℃ is investigated by small amplitude
oscillatory shear on a rotational rheometer. LDPE has higher viscosity
than PMVS at three temperatures, which affects the morphology and
rheological response of the blends. The LDPE-rich blends have smaller
dispersed droplets and longer relaxation time than the PMVS-rich blends.
Higher temperature means less viscosity as well as dynamic modulus
difference between the LDPE-rich blend and the PMVS-rich blend.
Increasing temperature fastens relaxation of polymer samples thus
relaxation time at higher temperature is shorter than that at low
temperature. Phase separation can be shown at some weight ratio of
PMVS/LDPE through the failure of time-temperature superposition
principle and double peaks of relaxation time including the form
relaxation time peak due to relaxation of dispersed droplets.
Keywords: Rheology; Blend; Relaxation Time; polymethylvinylsiloxane; Rheological Analysis; Viscosity; Elasticity
Abbreviations:
PMVS: Polymethylvinylsiloxane; LDPE: Low Density Polyethylene; PP:
Polypropylene; PA6: Polyamide 6; EPDM: Ethylene-Propylene-Diene; PCL:
Polycaprolactone
Introduction
In recent years rheology of polymer blends attracts
lots of researchers, and blending is an easy and convenient method to
obtain new and valuable polymer materials. Most blends are immiscible,
and the physical properties are affected by many factors such as weight
ratios, viscosity ratio, interfacial tension [1,2] and shear strength
etc. Rheological analysis is a powerful tool to relate the rheological
behavior and phase structure at different environments. In dynamic shear
on polymer blend, a balance between the breakup and coalescence affects
the morphology and rheological response. Coalescence mainly depends on
two parameters, one is the number of droplet collisions, another is the
ability of the blend to drain the film of matrix phase, which is
entrapped between two droplets of the dispersed phase until the critical
thickness for coalescence to happen is reached [3]. Increase of
concentration and droplet size of dispersed phase produces higher number
of droplets collisions. Two factors affect film drainage: interfacial
tension and viscosity of the matrix. Droplets with high viscosity are
easy to remain spherical during flow, while droplets with low viscosity
are likely to deform. Decrease of droplet coalescence will lead to
smaller particle size in compatibilized blends [4]. Droplets will
break when interfacial stress cannot counterbalance the shear stress
anymore.
Viscosity ratio of blend’s phases affects mainly the
dynamic modulus at low frequency since geometrical relaxation of the
droplets of dispersed phase brings about long-time relaxation.
Elasticity affects phase behavior of immiscible polymer blends besides
viscosity [5-7] and a corresponding model [8] has been developed to
describe elastic contribution to the interfacial tension. Rheology and
morphology of a polypropylene/polyamide 6 (PP/PA6) blends compatibilized
with maleic anhydride grafted polypropylene (PP-g-MAH) was investigated
by Shi et al. [9]. They found the morphology of the blend was of an
emulsion-in-emulsion type, i.e., PA6 particles dispersed in the PP
matrix themselves contained PP or PP-g-MAH inclusions. The
emulsion-in-emulsion morphology became visible when PA6 content was
high, for example, the ternary blend with PP/PP-g-MAH/PA6 was 35/35/30.
In our recent work [10], a polypropylene(PP)/ high density
polyethylene(HDPE) blend compatibilized with an Ethylene-Propylene-Diene
Monomer block copolymer(EPDM) has similar morphology and rheology. This
emulsion-in-emulsion structure is in How to cite this article: Hua Y L,
Ya Qian L, Chun L L, Guo L T. A Polymethylvinylsiloxane/Low Density
Polyethylene Blending Melt: Dynamic Rheological
0085 Behavior and Relaxation Time. Academ J Polym Sci. 2020; 3(5):
555621. DOI: 10.19080/AJOP.2020.03.555621
fact the so-called “core-shell”. A Core-shell morphology (core of
HDPE and shell of EPDM) in PP matrix for a polypropylene (PP)/
ethylene-propylene-diene (EPDM) rubber/high density polyethylene
(HDPE) 70/20/10 blend was successfully predicted by minimum
free energy model [11]. Also, another core-shell morphology
(core: HDPE, shell: EPDM-g-MA in PA6 matrix) was observed in
PA6/EPDM-g-MA/HDPE ternary blends [12].
Polymethylvinylsiloxane (PMVS) [13,14] is a material with
outstanding properties and has been widely used in industries,
such as thermal shielding, press pads, and weather resistance, etc.
The performance and radiation crosslinking of polycaprolactone
(PCL) and polymethylvinylsiloxane (PMVS) blends has been investigated
by Zhu and co-workers [15]. But researches on rheological
behavior on polymer blends about silicon rubber are not enough.
In this paper, dynamic rheological behavior and relaxation time of
a PMVS/LDPE binary blend were investigated. It was found viscosity
difference between the two components and temperature
affect greatly the morphology and rheological response, relaxation
time of the blends. The results are interesting and useful in
processing of silicon rubber materials.
Experimental
Materials and Methods
PMVS 110-2, manufactured by Jilin Jihui Industry and Commerce
Co., Ltd (Jilin, China). Its mass average and number-average
molar masses are Mw=570,000 g/mol and Mn =370,000g/mol,
respectively. LDPE 2102TN26 is produced by Qilu Petro. Co. Ltd(
Shandong China). Its mass average and number-average molar
masses are Mw = 190,000 g/mol and Mn = 23,000 g/mol, respectively.
Preparation of Blends
The materials were dried at 80 ℃ for 12h in an electric blast
drying oven, then were mixed in an internal mixer with the weight
ratio PMVS/LDPE of 10/90, 30/70, 50/50, 70/30 and 90/10 at
150 ℃ for 30minutes. The rotating speed of the internal mixer
was 30r/min. After that the samples were scraped off the internal
mixer, then were cooled down at room temperature. The sample
disks with diameter 25 mm and thickness 2mm for rheological
measurement were prepared by molding with a laboratory press
at 150 ℃ and under 10MPa for 10 min, and then cooled in the
atmosphere.
Measurement
Microscopic images: Melt the blending sample at 210 ℃ between
cover glasses on an electric stove and made into a piece of
film, then cooled the sample film to room temperature at nitrogen
atmosphere. Put the prepared film onto the objective table of a
polarization microscope and observed the microscopic photos at
unpolarized mode at proper magnification and save the photos on
a computer. The average dispersed phase size is calculated by a
software Nano Measurer 1.2.0. Rheological measurement: small amplitude oscillatory shear
was applied by using a rotational rheometer MCR301 made by Anton
Paar GmbH of Germany with two parallel plates. The diameter
of the plate is 25mm, the gap of the two plates was 1mm. The temperature
in the experiment was 150 ℃, 180 ℃ and 210 ℃, and the
angular frequency was from 0.028 rad·s-1 to 300 rad·s-1 in ascending
order. The measurement was under nitrogen gas to avoid the
oxidization of the samples. Before the start of the measurement
the samples were kept for 5min between the gap of the two plates
to eliminate thermal history. The linear viscoelastic regime was
determined by applying strain sweeping.
Results and Discussion
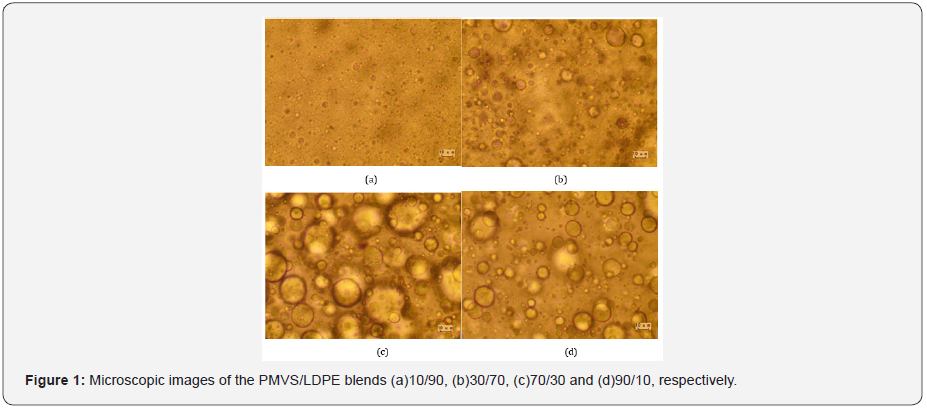
Figure 1 shows microscopic images of the PMVS/LDPE
blends with weight ratio 10/90, 30/70, 70/30 and 90/10, respectively.
The average diameter of the dispersed droplets is
14.0μm,19.54μm,7.16μm and 3.43μm, respectively. For the LDPErich
blends, such as 10/90 and 30/70, the matrix is LDPE and
the dispersed phase is PMVS. For the PMVS-rich blends, such as
70/30 and 90/10 blends, LDPE is the dispersed phase and PMVS
is the matrix. The viscosity of LDPE is much higher than that of
PMVS, as shown in Figure 2-4. Thus, it is much easier for PMVS to
breakup in LDPE matrix, and more difficult for LDPE to breakup
in PMVS matrix. In another word, the more viscous discrete LDPE
droplets in the 70/30 PMVS/LDPE sample are more easily to be
coarsened. The balance between the breakup and coalescence affects
the morphology and rheological response [16].
Figure 2-4 show the dynamic rheological behavior of the
PMVS/LDPE blending melts including the pure components PMVS
and LDPE at 150,180 and 210 ℃. At three temperatures LDPE has
higher viscosity than PMVS, and the viscosity of the blend decreases
as the weight ratio of the PMVS/LDPE increases except
the 50/50 blend. All the blends exhibit shear thinning behaviors
in the range of applied angular frequencies. As the temperatures
increases from 150 to 210 ℃, the viscosity of the blends drops,
and the viscosity of the LDPE-rich blend drops much faster than
the PMVS-rich blend, as shown in Figure 2-4. For example, the
10/90(PMVS/LDPE) blend has a viscosity of 21,000Pas,9040 Pas
and 5190 Pas at 0.028rad/s, while the 90/10(PMVS/LDPE) blend
has a viscosity of 6690Pas, 5010 Pas and 4780 Pas, respectively.
This is understandable, since LDPE is a branched polymer, and
PMVS is a liner polymer, the former is more sensitive to temperature
than the latter. Higher temperature means less viscosity difference
between the LDPE-rich blend and the PMVS-rich blend.
The dynamic modulus of the blend has similar behavior with the
viscosity. Due to the shape relaxation of discrete phase in the matrix,
the dynamic modulus of the blends present much more difference
at lower frequency, and the difference disappears gradually
at high frequency [17].
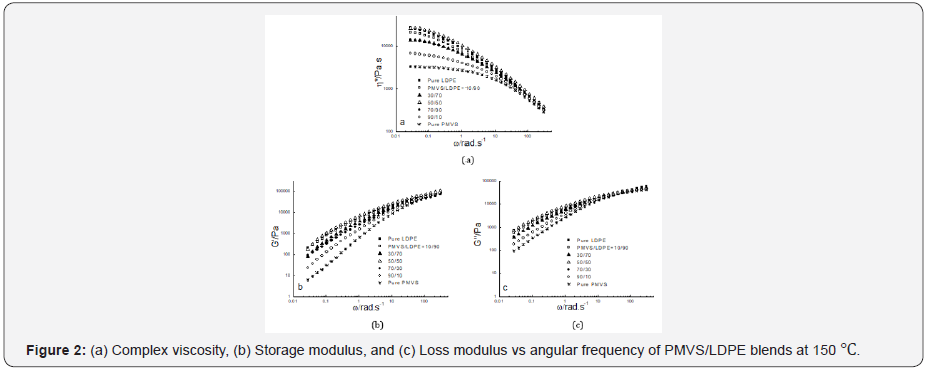
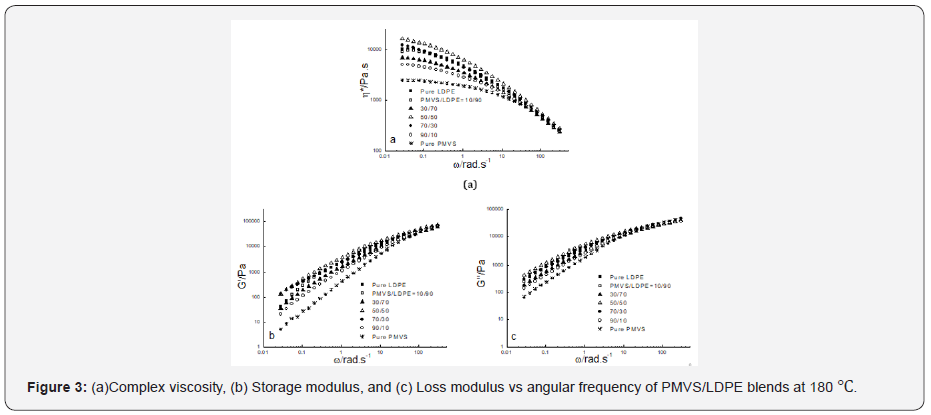
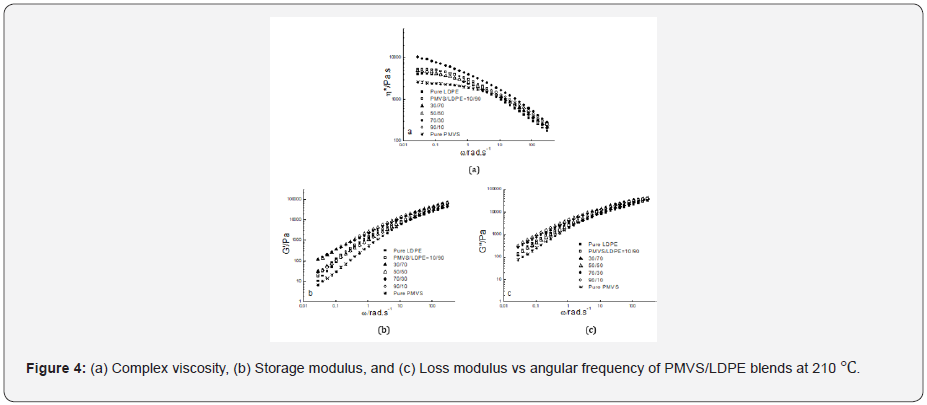
It is noticed the dynamic modulus of the 50/50 and 70/30
blend at low frequency is higher than that of pure PMVS and LDPE
at 180 ℃ and 210 ℃. This means these two blends are immiscible
[18,19]. The storage modulus of the two blends increases because
the interfacial area of the blends is changed by the relaxation and
deformation of dispersed phase droplets during dynamic rheological
measurement. Comparing the storage modulus curve and loss
modulus curve at three temperatures as shown in Figure 2-4, it
can be seen the loss modulus is higher than the storage modulus
at low frequency. The storage modulus is more sensitive to interfacial
tension than loss modulus at low frequency. It is worth mentioning
that the PMVS used in the blends is uncured sample and
can flow easily at high temperatures. Vulcanization can increase
the strength of the PMVS sample as well as the blends, which is
not the interest of this work [15,20].
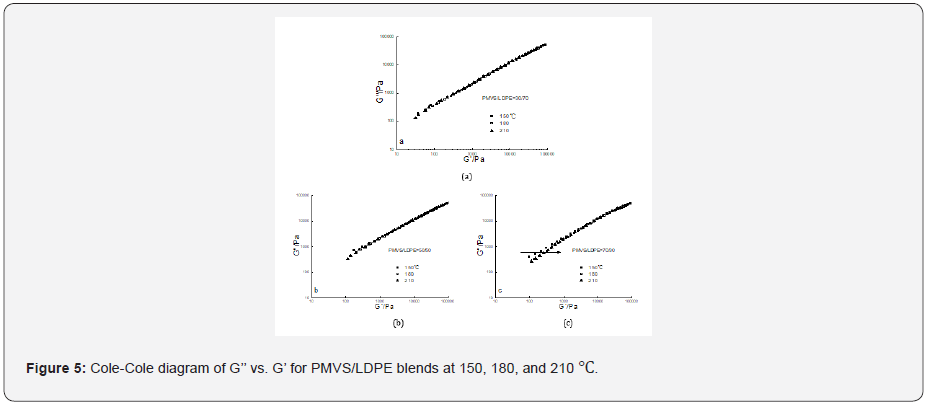
The Cole–Cole diagram G’’ versus G’ data at three temperatures
for the 30/70,50/50 and 70/30 PMVS/LDPE blends were
shown in Figure 5 respectively. It is obvious the G’’-G’ data at three
temperatures overlapped well for the 30/70 blend. But for the
50/50 blend the data at low modulus somewhat dispersed. The
dispersion phenomenon was more evident for the 70/30 blend.
The invalidity of time-temperature superposition principle means
phase separation of the blends [21]. As temperature increases, G’
value increases with a fixed G’’ (see the arrow in Figure 5c), which
has a similar trend to the work of Wu and co-workers [17]. The
estimated interfacial tension of PMVS/LDPE blend at 150,180 and
210 ℃ is 6.07,6.53 and 7.06mN/m respectively [22,23]. Thus, the
two polymers are immiscible. It is more difficult for more viscous
LDPE droplets to disperse in less viscous PMVS matrix. The 10/90
blend and 90/10 blend have similar trends with the 30/70, and
the 70/30 blend respectively, which are not shown in Figure 5.
Relaxation Time
Table 1 lists the characteristic frequency and relaxation time
of the blends when storage modulus(G’) equals to loss modulus
(G’’). The characteristic relaxation time is the reciprocal of the
characteristic frequency. Firstly, comparing the relaxation time of
pure component, it is clear that relaxation time of LDPE is longer
than PMVS at the same temperature. It can be acceptable since
LDPE has much higher viscosity than PMVS, as seen in Figure
2-4a. As the content of PMVS increases, relaxation time of the
PMVS/LDPE blends drops gradually at a fixed temperature. In another
word, the LDPE-rich blend has longer relaxation time than
PMVS-rich blend. As temperature increases, relaxation time of the
sample decreases because polymer chains relax faster at higher
temperature. The relaxation time listed in Table 1 is only some
characteristic relaxation time. In fact, polymer has a relaxation
time spectrum rather than one relaxation time. The weighted relaxation
time spectrum of the blending melts can be obtained by
using the approximation formula of dynamic modulus [24].
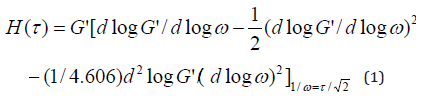

Figure 6 shows the weighted relaxation time spectrum of the
PMVS/LDPE blends. The shape of the spectrum curves at three
temperatures are similar but with different intensities. Higher
temperature corresponds to lower intensity. In order to analyze
the relaxation time spectrum of the blends at different temperatures,
(Table 2) lists the peak relaxation time. Basically, the LDPErich
blend has longer relaxation time than PMVS-rich blend. This
agrees with that shown in Table 1. The 50/50 and 70/30 blends
show two peaks of relaxation time at 180 and 210 ℃. The relaxation
time of the pure PMVS is about 0.13-0.18s. The relaxation
time of pure LDPE is about 2.56-18.68s at different temperatures,
as shown in Table 2. Some relaxation time listed in Table 2 is more
than 18.68s, it is neither that of PMVS nor of LDPE. This relaxation
time is the secondary peak, which corresponds to the longest form
relaxation time of dispersed phase droplets due to interfacial tension.
Appearance of two relaxation time peaks also means phase
separation of the blends, which is accordance with the failure of
time-temperature superposition principle shown in Figure 5.
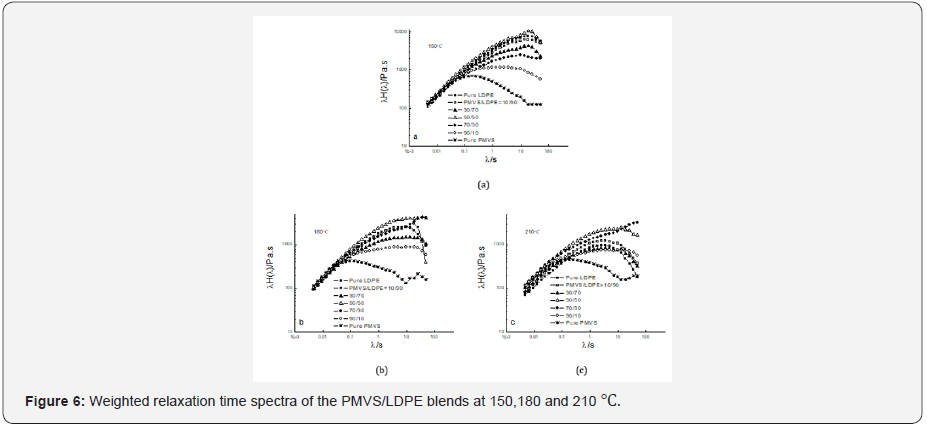
Not all the blends show the longest form of
relaxation time. In
the work of Shi and co-workers [25] with various PP/PA6 uncompatibilized
blends and PP/PP-g-MAH/PA6 compatibilized blends,
both PP and PA6 show individual relaxation time peak, and some
blends show a third peak at the longest time corresponded to the
form relaxation time. In the present work, PMVS/LDPE blends did
not show obviously individual peak relaxation time like that [26],
possibly because the two peak relaxation time merged together, even the
three peaks of relaxation time including the form relaxation
time merged. Relaxation time can also see from the peak of
dynamic viscosity (η’’ vs ω) curve [27]. It was reported [28]
interfacial
force between PP and PS was affected by addition of the
silica filler. Similar investigation about silica filler upon polymer
blends can be found in the literature [29-30].

Conclusion
Dynamic rheological behavior of the PMVS/LDPE blends at
150,180 and 210 ℃ is investigated through small amplitude oscillatory
shear. The more viscous LDPE is more difficult to breakup
in PMVS matrix, thus the LDPE-rich blends have smaller dispersed
droplets than the PMVS-rich blends. Higher temperature decreases
the viscosity difference between the LDPE-rich blend and the
PMVS-rich blend. The 50/50 and 70/30 PMVS/LDPE blends exhibit
invalidity of time-temperature superposition principle. Furthermore,
the LDPE-rich blends have higher viscoelasticity and
longer relaxation time than the PMVS-rich blends. The blends at
higher temperature have shorter relaxation time and lower relaxation
time spectrum. Some relaxation time spectrum of the PMVS/
LDPE blends show only one peak, the spectrums of the 50/50 and
70/30 PMVS/LDPE blends show a main peak and a longest form
relaxation time. These cases infer the PMVS/LDPE blends are immiscible.
To Know more about Academic Journal of Polymer Science
Click here: https://juniperpublishers.com/ajop/index.php
To Know more about our Juniper Publishers
Click here: https://juniperpublishers.com/index.php
Dr Ajayi have be a great doctor even know in the world, am here today tell the world my testimony about how i was cured from herpes i was having this deadly disease called herpes in my body for the past 4 years i but now i know longer have it again. i never known that this disease have a cure not until i meet someone know to the world called Dr Ajayi he cured me from herpes he have been great to me and will also be great to you too. i have work with other doctor but nothing come out. one day i did a research and came across the testimony of a lady that also have same disease and got cured by Dr Ajayi. then i contacted his email and told him my problem he told me not to worry that he have the cure i didn't believe him when he said so because my doctor told me there is no cure he told me i need to get a herbal medicine for the cure which i did and now am totally cured you can also be cure too if only you contact him via email ajayiherbalhome@gmail.com. you can also call or whatsapp his mobile number +234 815 472 4883.
ReplyDelete